Analyzing Process Capability and Process Capability Index in Quality Management
Analyzing process capability and process capability index to enhance efficiency and minimize defects.
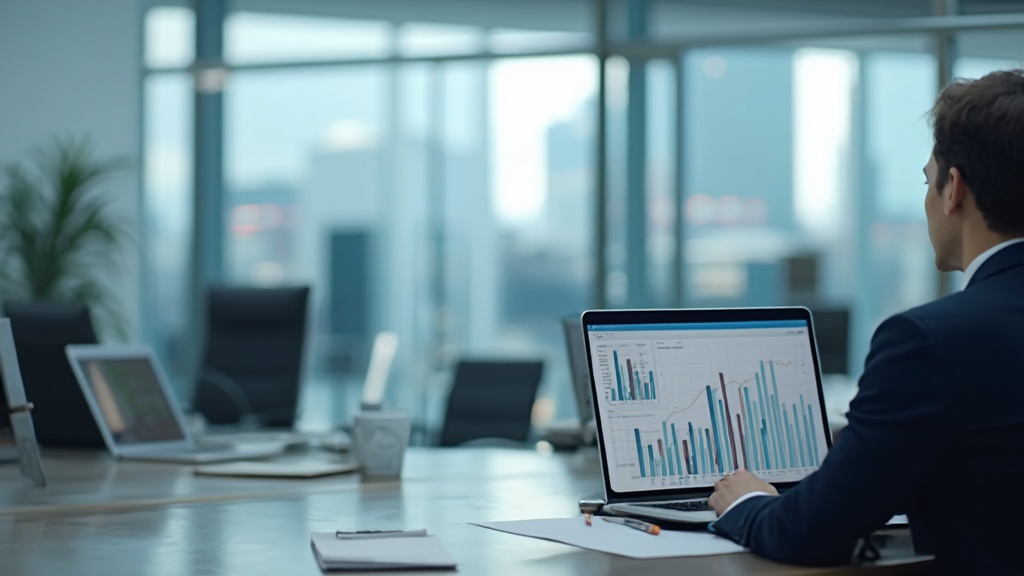
Introduction
In an ever-evolving manufacturing landscape, understanding and optimizing process capability is paramount to ensuring product quality and operational efficiency. Process capability indices, such as Cp, Cpk, Pp, and Ppk, quantitatively measure how well a process meets specified requirements, reflecting its precision and efficiency. The calculation of these indices involves meticulous data collection and analysis, comparing the inherent variability of the process with customer specifications.
Interpreting these indices provides critical insights into process performance, highlighting areas for potential improvement. In various industries, this analysis is indispensable for maintaining stringent quality control, validating changes, and enhancing customer satisfaction. Historical foundations like Shewhart's control charts and Deming's Total Quality Management (TQM) principles underscore the enduring significance of process capability analysis.
Furthermore, integrating advanced technologies and continuous improvement methodologies, such as Six Sigma and AI-driven predictive maintenance, plays a crucial role in refining process capability. By leveraging these tools, companies can systematically reduce variability, boost productivity, and achieve sustained excellence, as exemplified by industry leaders like Flex and Hitachi. This comprehensive approach to process capability not only ensures compliance with regulatory standards but also aligns with the dynamic advancements in manufacturing technologies and practices.
Understanding Process Capability Indices
Process performance evaluates how effectively a system can fulfill defined criteria and carry out its intended role. The performance metrics, including Cp, Cpk, Pp, and Ppk, offer a quantitative assessment of this ability. These measures contrast the fundamental variability of the operation with the customer's specifications, providing a clear indication of the operation's efficiency. An elevated performance measure indicates a more proficient system, which leads to a lower chance of creating flawed items. Highlighting accuracy and effectiveness, instruments such as electronic height gages are essential in attaining these high performance levels by delivering precise measurements and assessments throughout different manufacturing phases.
Calculating Process Capability
Determining the ability of a system starts with gathering information on its performance. This involves measuring output characteristics and determining both the mean and standard deviation. The following step is to compute performance measures, which combine these statistics with the upper and lower specification limits. For example, the performance measure (Cp) is calculated from the ratio of the specification range to variation in the method. Conversely, the performance measure (Cpk) considers how well the operation is centered within the specification limits, providing a more thorough perspective on its alignment and consistency.
Interpreting Process Capability Results
Interpreting capability results involves understanding what the indices reveal about the system. For instance, a Cp value greater than 1.0 indicates that the system is capable of producing within specifications. However, a Cpk value lower than Cp indicates that the operation is not well-centered, which could lead to a higher rate of defects. This distinction is essential, as not all simulations provide a comprehensive understanding of specific configuration settings. Often, a combination of different simulations is necessary, with outputs from one serving as inputs for another, creating a sequence of simulations. This intricate manual planning requires thorough assessment of time, cost, and outcome to select the optimal scenario for enhancement.
Applications of Process Capability
'Capability analysis is a vital instrument in quality management, utilized widely across sectors to guarantee product quality and efficiency in operations.'. This analytical approach assists organizations in identifying areas that require enhancement, confirming modifications, and upholding strict oversight over production activities. By conducting regular evaluations, companies can significantly enhance customer satisfaction, minimize waste, and optimize overall operational performance.
For example, in the document 'Semantic Capability Model for the Simulation of Manufacturing Procedures,' it is emphasized that simulations play a vital role in exploring and comprehending the intricate details of manufacturing activities. The combination of different simulations often provides a more comprehensive understanding, which is crucial for making informed decisions about process improvements.
Moreover, the importance of maintaining high standards in manufacturing, especially in sectors like medical device production, cannot be overstated. Ensuring that devices meet regulatory standards is essential for patient safety and product efficacy. Following good manufacturing practices (GMP) and international standards like ISO 13485 and FDA regulations demonstrates the strict nature of control in this field.
The emphasis on excellence and efficiency isn't new. Historical figures like Shewhart and Deming laid the groundwork with concepts like control charts and Total Quality Management (TQM), which are still relevant today. In recent times, the use of advanced technologies such as AI for predictive performance management has further improved these methods, making them more accurate and efficient.
In conclusion, consistent evaluation of operational effectiveness not only helps in sustaining control and enhancing standards but also aligns with the changing environment of manufacturing technologies and norms.
Improving Process Capability
Improving operational effectiveness includes various strategies, such as refining design, enhancing worker training, and applying better quality control measures. Utilizing methodologies such as Six Sigma and continuous improvement can systematically reduce variability and enhance performance. For instance, Flex's use of AI for predictive maintenance in their Zalaegerszeg facility has significantly improved the accuracy and productivity of their printed circuit board assemblies (PCBAs), which are essential for nearly every electronic product. Regular monitoring and analysis of performance indices are crucial in guiding these improvement efforts, ensuring sustained excellence. As Hitachi shows with its advanced IT offerings and automation solutions, optimized business operations result in improved productivity and a greater return on investment (ROI). These examples underscore the value of integrating advanced technologies and continuous monitoring to maintain and elevate process capability.
Conclusion
Optimizing process capability is essential in today's competitive manufacturing environment. Capability indices such as Cp, Cpk, Pp, and Ppk serve as vital metrics for evaluating how well processes meet specified requirements. By comparing process variability with customer specifications, these indices provide insights into operational efficiency and product quality, with tools like electronic height gauges ensuring precision.
The calculation of these indices involves careful data collection and analysis, allowing organizations to reflect on their process performance. Understanding the differences between Cp and Cpk is crucial, as it highlights areas for improvement and ensures processes remain centered within specification limits.
Process capability analysis is widely utilized across various industries, playing a key role in quality management. Regular evaluations not only help maintain stringent manufacturing controls but also enhance customer satisfaction and reduce waste. The foundational contributions of figures like Shewhart and Deming continue to be relevant, further supported by advancements such as AI-driven predictive maintenance.
To enhance process capability, organizations must adopt a multifaceted approach that includes refining process design, improving operator training, and implementing robust quality control measures. Utilizing methodologies like Six Sigma and consistently monitoring capability indices enables systematic reductions in variability and performance enhancement. The success of industry leaders illustrates the importance of integrating advanced technologies and continuous improvement to achieve sustained excellence in manufacturing.