Understanding Defects in Products: Classification, Causes, and Impact
Understanding defects in products: types, causes, and their impact on consumer safety and manufacturer liability.
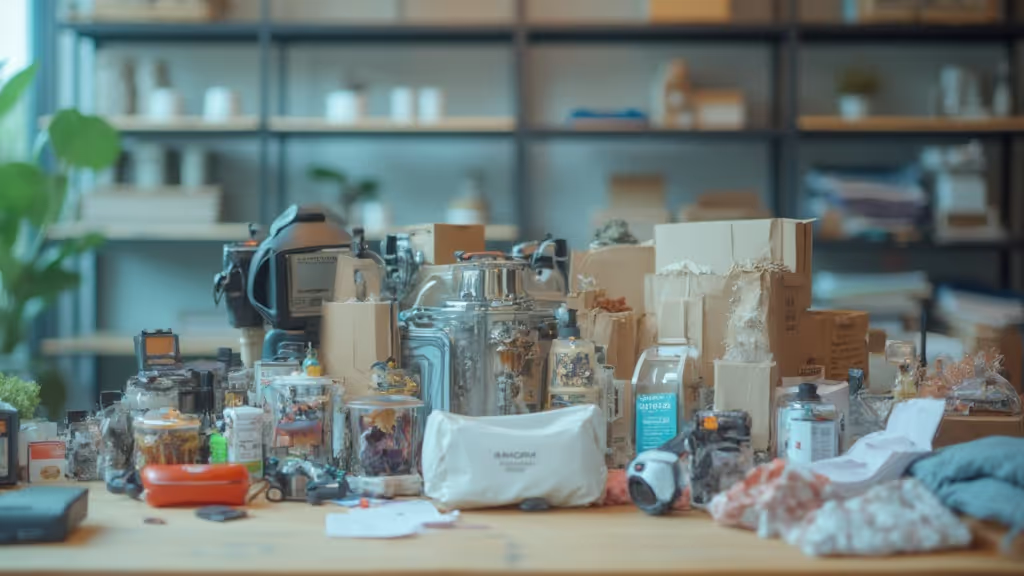
Introduction
In the world of manufacturing and consumer products, understanding the nuances of product defects is crucial. These defects can be broadly categorized into three main types: design defects, manufacturing defects, and marketing defects, each carrying unique characteristics and implications for both consumers and manufacturers. Design defects are inherent flaws in a product's blueprint, making it unsafe or unfit for its intended use.
Manufacturing defects occur during the production process, resulting in deviations from the intended design due to errors or substandard materials. Marketing defects involve issues with how a product is presented, such as insufficient instructions or misleading advertising.
Each type of defect poses significant risks and challenges, necessitating robust quality control measures and regulatory compliance strategies. By delving into the root causes of these defects, manufacturers can implement more effective solutions to enhance product safety and consumer trust. This article explores the various types of product defects, their causes, and their far-reaching impacts, providing a comprehensive understanding that is essential for maintaining high standards in product development and consumer protection.
Types of Product Defects
Product flaws can be broadly categorized into three main types: design issues, manufacturing problems, and marketing errors. Each category carries unique characteristics and implications for both consumers and manufacturers.
Design shortcomings occur when there is a fundamental flaw in the item's design, rendering it inherently unsafe or unsuitable for its intended use. These flaws exist before the item is even created. A notable instance is the recurring recalls in the baby formula industry, where design flaws in the formulation led to significant safety concerns and a lack of availability, highlighting the critical need for meticulous design processes.
Manufacturing issues arise during the production process and lead to items that stray from the intended design, often due to mistakes in assembly or the use of inferior materials. This type of defect is particularly prevalent in highly regulated industries such as food, drugs, and medical devices. For instance, the occurrence of product withdrawals in pet food—twice as many as baby formula withdrawals over the past five years—underscores the importance of stringent manufacturing controls and quality assurance practices. As highlighted by Matthew M. Lowe, Chief Product & Marketing Officer at MasterControl, manufacturing systems are not free from errors, and recalls serve as an essential mechanism for ensuring safety and maintaining confidence in items.
Marketing flaws involve problems with how an item is promoted, such as inadequate instructions, absence of safety warnings, or deceptive advertising. These issues can result in user misapplication and possible injury. Guaranteeing clear, precise, and thorough details about items is essential for avoiding such issues and safeguarding public safety.
Grasping these classification types assists producers in applying more efficient quality assurance techniques and regulatory adherence strategies, ultimately improving safety and consumer confidence.
Design Defects
'Design shortcomings arise when a product's blueprint has inherent flaws, making it unsafe or ineffective for its intended purpose.'. Such issues often arise from inadequate planning, insufficient testing, or a failure to consider user needs comprehensively. For instance, toys that can easily break and pose choking hazards are classic examples of design defects. Implementing a strategic Human-Factors Engineering (HFE) and Usability Engineering (UE) Plan is crucial to mitigating these risks. By centering the design process around the user's experience, manufacturers can address potential issues before they become serious hazards. This approach involves answering critical questions such as: Who are the users? What are the intended uses of the item? In what environment will the item be deployed?
Manufacturing Defects
Manufacturing flaws occur during the production process when products differ from their intended design. These flaws can arise from various sources, including human error, machinery malfunctions, or substandard materials. Traditional quality control methods, which heavily rely on human inspection, often exacerbate these issues. Manual inspections are slow and laborious, leading to production bottlenecks. Furthermore, human judgment can be subjective and inconsistent, resulting in unnoticed imperfections.
For instance, in the production of electronic devices, inspectors might overlook minor issues such as faulty wiring or soldering errors, which can later lead to the complete batch failing. The limitations of traditional quality control methods highlight the need for more advanced solutions. State-of-the-art technologies, like AI-powered flaw detection systems, provide instant and accurate recognition of even the most subtle imperfections, greatly enhancing manufacturing efficiency and item quality.
Marketing Defects
'Marketing issues relate to how a product is showcased to buyers, including deceptive information, insufficient warnings, or incorrect labeling.'. Such flaws can result in user misuse and possible injury. A prime example is the American Gas Association (AGA) and natural gas utilities, which have historically downplayed the health risks associated with gas stoves by funding studies that cast doubt on emerging scientific evidence. This approach mirrors tactics used by the tobacco industry to fend off regulation by emphasizing uncertainty in health research. In another instance, Philips Respironics faced backlash after recalling sleep apnea devices due to toxic emissions, only to later claim that new tests showed no long-term health risks. These cases underscore the critical importance of transparent marketing practices to ensure consumer safety and trust.
Causes of Product Defects
Product flaws emerge from a variety of origins, each playing a role in the overall decline in the quality of goods. Among the primary culprits are human errors, which can occur due to deviations from work instructions or outdated processes. Quality control issues are another significant factor, often stemming from the limitations of traditional methods. These methods can be bottlenecked by inefficiency, subjectivity, and limited scope, making it difficult to consistently identify flaws.
Material and component failures also play an essential role, where low-quality materials or design flaws compromise the product's integrity. External contamination, whether from environmental conditions or storage methods, further exacerbates these issues. For instance, geopolitical tensions and logistical challenges have recently highlighted the fragility of global supply chains, intensifying the risk of issues.
Identifying the root causes of these flaws is paramount. As one expert notes, 'The significance of any problem is the relative value the primary effect has on you or your organization.' By conducting a thorough Root Cause Analysis (RCA), businesses can pinpoint specific issues and implement targeted corrective actions. This process is essential not only for addressing current issues but also for preventing their recurrence, ensuring that solutions are both effective and sustainable.
Impact of Product Defects
Product defects can have profound implications, affecting consumer safety, financial stability of manufacturers, and legal accountability. In recent years, there have been notable withdrawals, such as the widely reported baby formula shortages that left many parents searching for safe options. Interestingly, pet food withdrawals have taken place twice as frequently as those for baby formula in the last five years, yet they receive less media attention. This disparity can be attributed to the scale of production; the baby formula market is dominated by a few manufacturers, making any withdrawal more impactful.
Production mistakes are unavoidable, and product returns act as an essential method for guaranteeing buyer safety. These withdrawals not only safeguard buyers but also influence trust levels in products more than many understand. Highly regulated industries like food, drugs, and medical devices invest heavily in quality control to avoid the financial and reputational damage associated with recalls. This investment forms a virtuous cycle, as seen in the development of comprehensive quality control systems aimed at minimizing defects.
Legal ramifications are also evolving. The European Commission's suggestion to revise the Liability Directive demonstrates the necessity to tackle contemporary technological progress, guaranteeing equitable recompense for victims of faulty items and improving consumer safety. This proposal underscores the importance of durable, reusable, and upgradable products, highlighting the continuous evolution of product liability laws to keep pace with technological advancements.
Conclusion
Understanding the various types of product defects—design, manufacturing, and marketing—provides essential insights into the complexities of product development and consumer safety. Design defects stem from inherent flaws in a product's blueprint, which can lead to significant safety hazards if not addressed during the planning phase. Manufacturing defects arise during production, often due to human error or substandard materials, emphasizing the necessity for advanced quality control measures.
Marketing defects highlight the importance of transparent communication, as misleading information can lead to consumer misuse and potential harm.
The causes of product defects are multifaceted, including human error, outdated processes, and material failures. Identifying these root causes through thorough analysis is critical for implementing effective corrective actions. The impact of product defects extends beyond individual safety concerns, affecting manufacturers' financial stability and legal accountability.
High-profile recalls, such as those in the baby formula and pet food industries, illustrate the potential risks and the importance of maintaining rigorous quality control practices.
In summary, a comprehensive understanding of product defects is vital for manufacturers aiming to enhance product safety and consumer trust. By prioritizing robust quality control measures and transparent marketing practices, organizations can not only mitigate risks but also foster a culture of accountability and continuous improvement. This strategic approach ultimately benefits consumers and manufacturers alike, paving the way for safer products and greater market confidence.