Understanding the Production Part Approval Process: A Comprehensive Overview
Explore the essentials of the production part approval process for quality and compliance in manufacturing.
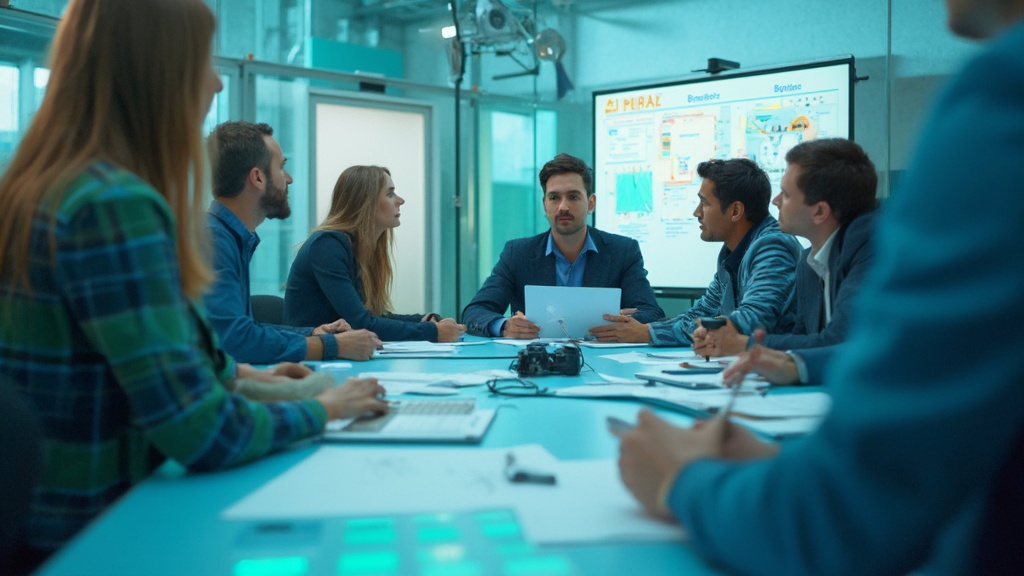
Introduction
The Production Part Approval Process (PPAP) serves as a cornerstone in the manufacturing sector, particularly within industries where precision and compliance are paramount. This systematic approach ensures that suppliers can consistently deliver parts that meet established design specifications and quality standards. Not merely a procedural formality, PPAP acts as a crucial validator of both the manufacturing process and the product itself, significantly mitigating risks associated with defects.
In highly regulated fields such as medical device manufacturing, where adherence to guidelines like ISO 13485 and FDA regulations is non-negotiable, the importance of a robust PPAP becomes even more evident. By enhancing operational excellence and fostering trust between suppliers and customers, effective implementation of PPAP not only safeguards product quality but also strengthens market competitiveness. This article delves into the purpose, key elements, and common challenges of PPAP, offering insights into its role in maintaining rigorous standards across the manufacturing landscape.
What is PPAP?
The Production Part Approval Process serves as an essential structure in production, especially for sectors that emphasize accuracy and adherence, like automotive and aerospace. This standardized procedure is intended to verify that a supplier's production method can consistently generate parts that align with design specifications and quality standards.
The process is not just a procedural step; it serves as a crucial validator of both the production process and the product itself before the start of full-scale production. By effectively scrutinizing each phase of production, the process helps mitigate risks associated with product defects and ensures that the final output meets stringent regulatory standards. This is crucial in sectors like medical device production, where compliance with regulations such as ISO 13485 and FDA guidelines is imperative.
The intricacy of the qualification procedure in medical device manufacturing highlights the significance of Production Part Approval. Challenges like regulatory constraints and confidentiality concerns can hinder efficiency. Yet, a strong production part approval process can streamline this qualification procedure, enhancing operational excellence and ensuring that products are safe and effective for consumers. Consequently, firms that diligently apply the process not only improve their standing but also foster confidence with their clients, ultimately resulting in heightened market competitiveness.
Purpose of PPAP
The primary objective of the Production Part Approval Process (PPAP) is to ensure that suppliers fully comprehend customer requirements and possess the capability to produce products that consistently meet those standards. This process functions as a vital communication bridge between suppliers and customers, aligning both parties on crucial aspects such as production quality, reliability, and delivery timelines.
In today's production environment, characterized by increasing complexity and diversity in products—from simple consumer items to sophisticated medical devices—ensuring compliance with rigorous standards is more critical than ever. For instance, medical device manufacturing adheres to Good Manufacturing Practices (GMP) and stringent regulations like ISO 13485 and FDA requirements. These frameworks not only enhance product efficacy but are also essential for safeguarding patient safety.
Moreover, effective supplier relationship management plays a significant role in the overall success of product development. Trust, transparency, and open communication are key factors that strengthen these relationships. For example, collaborative discussions regarding cost can lead to price reductions and more efficient production processes. By engaging in proactive relationship management, companies can streamline their operations and mitigate risks associated with production inconsistencies.
Ultimately, this process is not merely a procedural formality; it is a vital component of a wider strategy to promote quality and reliability in the supply chain, which is essential for sustaining a competitive edge in a saturated market.
Key Elements of PPAP
The Production Part Approval Process (PPAP) is a critical framework for ensuring quality and compliance in manufacturing, particularly in the medical device industry. 'This procedure encompasses several essential components that collectively provide a detailed overview of the production cycle.'. Essential components consist of design records, which outline the specifications and requirements for the product; engineering change documents that record any modifications made during development; and flow diagrams that depict the sequence of operations involved in production.
Control plans are another crucial element, detailing the measures in place to monitor and manage production activities effectively. 'Measurement system analyses are conducted to evaluate the precision and reliability of measurement tools used throughout the production stages, ensuring that data collected is both accurate and meaningful.'. Capability studies evaluate if a production method can reliably generate outcomes that satisfy established specifications.
Each of these components plays a crucial role in establishing a comprehensive quality management system. By thoroughly documenting and understanding these elements, manufacturers can effectively navigate the complex landscape of regulatory compliance. For instance, adherence to Good Manufacturing Practices (GMP) is essential, as highlighted in the stringent guidelines set by the FDA and ISO 13485 standards. These regulations are not merely bureaucratic necessities; they are fundamental to ensuring patient safety and product efficacy, thereby enhancing overall operational excellence in the manufacturing process.
Common Challenges and Solutions in PPAP
Implementing the Production Part Approval Process (PPAP) can present various challenges, particularly in terms of documentation complexity and the differing requirements across industries. Suppliers often face difficulties in gathering the comprehensive data necessary for adherence, which can be exacerbated by a lack of familiarity with customer-specific standards.
To mitigate these issues, it is essential to establish clear guidelines that articulate the documentation process and requirements. For instance, developing a structured framework for submissions can enhance understanding and adherence. Sophisticated digital tools can also be crucial in simplifying documentation by allowing quick data extraction and gap analysis. This shift towards automation is critical, especially given the diverse approaches and systems currently employed across the industry.
Regular communication channels should be established to facilitate ongoing dialogue between suppliers and customers. Such interactions not only address immediate concerns but also foster a collaborative environment that encourages knowledge sharing and problem-solving. As noted by industry experts, ensuring effective integration of digital quality measures with existing processes is crucial. This includes defining clear objectives and developing a phased implementation plan that builds on previous successes, thereby enhancing overall operational efficiency.
With regulatory demands becoming increasingly stringent, it is vital to stay ahead by adopting these proactive measures. Streamlining regulatory document preparation can significantly reduce delays and errors, which are often exacerbated by the complexities of packaging and labeling. By taking a comprehensive approach to PPAP implementation, suppliers can ensure both compliance and product quality, ultimately contributing to a more resilient supply chain.
Conclusion
The Production Part Approval Process (PPAP) is vital for maintaining quality and compliance in manufacturing, particularly in precision-driven sectors like automotive and medical devices. By ensuring that suppliers can consistently produce parts that meet stringent specifications, PPAP effectively mitigates risks associated with product defects.
Beyond compliance, PPAP acts as a crucial communication link between suppliers and customers, fostering alignment on quality and reliability. This is increasingly important in a complex manufacturing environment, where strong supplier relationships can enhance operational efficiency and market competitiveness.
Key elements of PPAP, such as design records, control plans, and capability studies, form the backbone of a robust quality management system. These components help ensure adherence to regulatory requirements and facilitate the consistent delivery of high-quality products. Addressing challenges like documentation complexity through clear guidelines and advanced digital tools can streamline the PPAP process, improving overall effectiveness.
In summary, the successful implementation of PPAP is essential for safeguarding product quality and building trust within the supply chain. Organizations that prioritize this rigorous process not only comply with stringent regulations but also strengthen their competitive position in the market. A commitment to a robust PPAP underscores an organization's dedication to quality, safety, and customer satisfaction, ultimately contributing to a resilient supply chain.