Exploring the Latest Innovations in NDE/NDT for Quality Control and Manufacturing Insights
Explore NDE/NDT innovations for quality manufacturing insights.
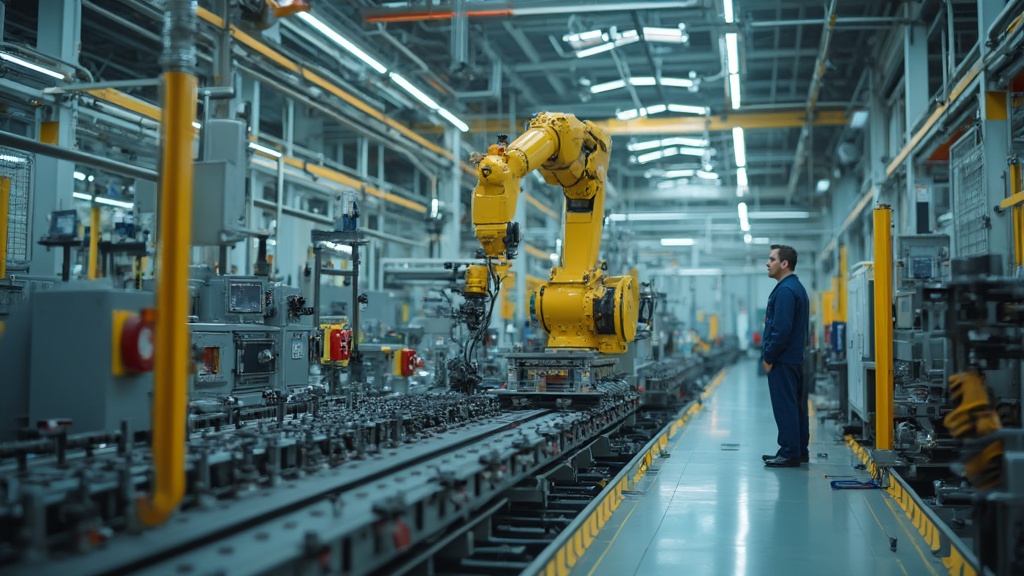
Introduction
Non-Destructive Evaluation (NDE) and Testing (NDT) are integral to maintaining product integrity and reliability in manufacturing. These techniques play a pivotal role in identifying defects and inconsistencies without causing damage, ensuring product quality and safety. NDE/NDT is widely applied across various sectors, including automotive, aerospace, and oil and gas.
As industries strive for innovation and sustainability, the shift towards mono-material construction and thermoplastic composites highlights the importance of choosing the right materials and considering the entire production lifecycle. Additionally, the rapid convergence of Operational Technology (OT) and Information Technology (IT) brings forth cybersecurity concerns that need robust measures. NDE/NDT is more than just a testing protocol; it is a comprehensive approach that contributes to smarter, safer, and more sustainable manufacturing processes.
Key Applications of NDE/NDT in Manufacturing
Non-Destructive Evaluation (NDE) and Testing (NDT) are crucial in ensuring the integrity and reliability of products. These methods are skillfully applied to identify defects and inconsistencies in materials and structures sans damage. The versatility of NDE/NDT is evident across automotive, aerospace, oil and gas sectors, among others. As we delve into these techniques, we recognize their pivotal role in safeguarding product quality and safety.
As industries strive for innovation and sustainability, Mono-material construction and thermoplastic composites are reshaping production landscapes. The shift to a uniform polypropylene cap, for instance, not only enhances recyclability but also indicates a move towards more sustainable practices. It is essential to choose the right materials and remain vigilant about the entire production lifecycle, from design to disposal.
Moreover, with the rapid convergence of Operational Technology (OT) and Information Technology (IT), cybersecurity emerges as a critical concern. Industry 4.0 introduces both efficiencies and vulnerabilities, necessitating robust cybersecurity measures to protect networked machines from potential breaches.
Overall, the implementation of NDE/NDT is more than just a testing protocol; it is a comprehensive approach that contributes to the evolution of smarter, safer, and more sustainable production processes, reflecting a commitment to excellence and forward-thinking in an increasingly interconnected world.
Advancements in NDE/NDT Technologies
Nondestructive Evaluation (NDE) and Nondestructive Testing (NDT) methods are leading the way in ensuring product reliability and safety in manufacturing. Advancements in these fields are reshaping the landscape of quality control. Computed Tomography (CT) and Digital Radiography (DR) have pushed the boundaries of imaging, enabling precise internal structure analysis without disassembling products. Ultrasonic Testing (UT), enhanced by the Total Focusing Method (TFM), has significantly improved defect detection and characterization, resulting in more accurate assessments.
Artificial Intelligence (AI) is another transformative force in NDE/NDT, offering the ability to analyze vast datasets and identify patterns that may elude human inspectors. Its implementation, however, should be carefully aligned with business objectives and consider the tool's fit for specific needs. As Kevin Becker wisely puts it, "All models are wrong; some models are useful."
Guided Wave Testing (GWT) has provided a means to inspect large areas and complex geometries from a single test point, streamlining the inspection and reducing downtime. Producers aiming to incorporate these digital methods seamlessly must establish distinct objectives and a gradual implementation plan, as opposition to alteration and technological proficiency among staff members are common challenges.
The successful implementation of these advanced NDE/NDT methods also depends on efficient data interoperability among design, engineering, and operational systems, ensuring a coherent and streamlined production procedure. By embracing these innovations, manufacturers can not only enhance quality control but also position themselves competitively in an evolving industrial landscape.
Emerging Trends in NDE/NDT
In the realm of Non-Destructive Evaluation (NDE) and Non-Destructive Testing (NDT), two significant trends are making waves: the use of Augmented Reality (AR) and Virtual Reality (VR), and advancements in Eddy Current Testing (ECT) and Phased Array Ultrasonics. These innovative advancements are not just reshaping the inspection procedure but are also establishing fresh benchmarks in effectiveness and flaw identification.
AR and VR advancements are causing a significant change in manufacturing inspections. AR, for instance, integrates digital information with the user's environment in real time, typically through smart glasses or tablets. This blend of virtual and real-world elements allows for a more interactive and enhanced inspection process. The technology lays out 3D models, detailed instructions, and vital data right before the user's eyes, making it easier to spot defects and conduct thorough analyses. It's like having an expert by your side, providing continuous guidance and assessment, optimizing both safety and quality.
The influence of AR in production is significant, with data indicating that it speeds up the onboarding of new employees in intricate assembly environments. This is crucial, considering the aging workforce and the loss of specialized skills as seasoned professionals retire. AR serves as both a coach and an assistant, offering real-time advice and risk assessment, thereby speeding up the learning curve without compromising on safety or product standards.
ECT and Phased Array Ultrasonics represent the next leap in inspection methods, moving beyond traditional manual and X-ray techniques. These methods offer more detailed insights into the internal structure of materials, allowing for early detection of potential problems and shifting maintenance strategies from reactive to predictive.
The development of these advancements is in harmony with the ideas of visionary personalities like Emanuel Swedenborg, who centuries ago presented a plethora of scientific insights and inventions. Today, their innovation ethos continues to motivate progress in NDE/NDT, guaranteeing that control of production standards keeps up with the intricacies of contemporary production and the elevated expectations in today's market.
Benefits of NDE/NDT Innovations for Quality Control and Manufacturing
The combination of Non-Destructive Evaluation (NDE) and Non-Destructive Testing (NDT) methods is revolutionizing the field of control and production, offering a range of advantages that go beyond conventional approaches. These advancements serve as a cornerstone for early detection of defects and irregularities, which is crucial in maintaining not just the overall excellence of products but the entire spectrum of the manufacturing process—from design to delivery. Adopting NDE/NDT methodologies implies embracing a holistic approach to excellence, similar to the comprehensive comprehension of superiority in Japanese industry, where it penetrates all facets of production and management.
Utilizing such technologies leads to precision in identifying potential issues before they become costly problems, ensuring the final product meets the highest standards of excellence. It's a strategy that aligns with the vision of a future where digital excellence meshes seamlessly with existing systems, as underscored by industry experts. By establishing distinct objectives, manufacturers can incorporate digital quality into their operations without interrupting established workflows, ultimately attaining a balance between innovation and reliability.
Using a gradual method for execution, as suggested by experts in the field, manufacturers can enhance the achievements of already digitized stages, laying the groundwork for a strong basis for future procedures. This strategic integration is crucial in the face of evolving workplace dynamics, as evidenced by companies like Atlassian, where a staggering 92% of staff find work flexibility integral to their best performance.
Moreover, the application of augmented reality (AR) in manufacturing exemplifies the convergence of digital innovation and operational efficiency. AR allows for the overlay of virtual elements such as 3D models and data onto the real-world environment, enhancing the precision and efficiency of tasks performed by workers equipped with AR-enabled devices.
In the realm of environmental responsibility, the incorporation of green innovation within quality control processes is pivotal. Research on supply chain inventory models incorporating green practices to curb carbon emissions reveals a comprehensive approach to profit maximization while mitigating environmental impact. This method involves meticulous inspection and rework strategies, underscoring the importance of precision and sustainability in modern manufacturing.
The culmination of these factors—from AR to green technologies and the strategic integration of digital quality—is a testament to the transformative power of NDE/NDT innovations. They are not just tools for upholding high standards but instruments for nurturing a culture of excellence that penetrates every aspect of a product's lifecycle, ensuring customer satisfaction and brand loyalty.
Case Studies: Successful Implementation of NDE/NDT Innovations
Non-destructive Evaluation (NDE) and Non-destructive Testing (NDT) have transformed quality control and production processes across various industries. By examining real-world applications, we gain insights into their transformative impact. GE Aerospace, with over a century of powering aircraft, relies on NDE/NDT to ensure the reliability of their jet engines. Their commitment to innovation has led them to lead the charge in achieving net-zero CO2 flight emissions, underscoring the role of advanced testing in sustainable manufacturing.
In Dubai, RoboDK's digital twin is leading the way in robotics innovation. By creating a virtual counterpart to a physical robotic system, they are able to optimize production processes and preempt maintenance needs, thereby enhancing productivity without interruption. In the same way, researchers from Western Washington University utilized digital replica innovation in production to establish a simulated learning factory that complements the physical setup, streamlining the production lifecycle and enhancing efficiency.
These examples highlight the significance of NDE/NDT in driving data-driven innovation. The adoption of AI, advanced computing, and machine learning is not only shaping industrial asset management but also engineering 'serendipitous moments' in various sectors, including healthcare. With the establishment of accurate baselines for asset health, organizations can shift from reactive maintenance to predictive strategies, minimizing service disruptions and maximizing asset longevity.
As we look towards the future, the integration of NDE/NDT in various business domains is anticipated to deliver more streamlined, accurate, and sustainable solutions. The proof is evident: these innovations are not only about upholding standards but are crucial in the ongoing development of control and production insights in Asia and beyond.
Future Prospects and Integration of NDE/NDT Innovations
The scope of Nondestructive Evaluation (NDE) and Nondestructive Testing (NDT) is widening, offering the potential to transform quality control and production processes with state-of-the-art methodologies. As we delve into the future of NDE/NDT, we find ourselves at the confluence of Artificial Intelligence (AI), Robotics, and the Internet of Things (IoT) - each bringing its own set of enhancements to defect detection, predictive maintenance, and manufacturing efficiency.
At the heart of these advancements lies the incorporation of AI, which is not simply about embracing new methods but aligning them with business objectives. Ai's ability to process and analyze vast amounts of data can lead to more accurate predictions and timely maintenance, minimizing downtime and ensuring consistent production quality. Robotics, too, plays a pivotal role, with applications such as the innovative system created by Dubai's Robotics Lab using RoboDK's digital twin advancements. This innovation offers a virtual representation of physical robotic systems, enabling accurate duplication and simulation of tasks without the requirement for expensive prototypes or interruptions to the production line.
Moreover, the IoT furthers this integration by interconnecting various components of the manufacturing process, offering real-time monitoring and data exchange. This connectivity is crucial for modernizing data systems, bridging the gap between operational technology (OT) and information technology (IT), and enhancing interoperability across engineering, design, and factory operations. These progressions are not only conceptual; they mirror the ongoing discussions about electrification systems, energy generation methods, and sustainability, as emphasized in The Current's news and GE's Cutting Carbon podcast.
Continuous research and development in NDE/NDT are paramount to overcoming the challenges of a rapidly evolving industry. Manufacturers must embrace a structured approach to digital excellence, as highlighted by MTI's insights on establishing distinct objectives, achievable targets, and a phased implementation plan. A concentrated and goal-oriented approach ensures that the integration of digital excellence with existing systems is seamless, overcoming common challenges such as resistance to change and the need for workforce technological proficiency.
To sum up, the future of NDE/NDT is not only about the implementation of new methodologies; it's about strategic integration, ongoing enhancement, and aligning with the constantly evolving manufacturing and control landscape. The potential for these technologies to enhance efficiency and ensure product quality is immense, provided that they are implemented thoughtfully, with a clear vision for their role within the broader system.
Conclusion
In conclusion, NDE/NDT techniques are vital for maintaining product integrity and reliability in manufacturing. They identify defects without causing damage, ensuring product quality and safety across industries like automotive, aerospace, and oil and gas.
The shift towards mono-material construction and thermoplastic composites highlights the importance of choosing the right materials and considering the entire production lifecycle. NDE/NDT enables informed decisions, enhancing recyclability and promoting sustainability.
The convergence of OT and IT brings cybersecurity concerns, and NDE/NDT plays a significant role in securing networked machines. It is a comprehensive approach that contributes to smarter, safer, and more sustainable manufacturing processes.
Advancements in NDE/NDT technologies like CT, DR, UT, AI, and GWT improve defect detection and analysis, enhancing quality control and competitiveness.
Emerging trends in NDE/NDT, such as AR, VR, ECT, and Phased Array Ultrasonics, redefine the inspection process. AR and VR enhance precision and efficiency, while ECT and Phased Array Ultrasonics enable early detection and predictive maintenance.
The integration of NDE/NDT innovations brings benefits like early defect detection and meeting high standards of excellence. Strategic integration of digital quality technologies like AR and green technologies enhances precision, efficiency, and sustainability.
Real-world case studies demonstrate the transformative impact of NDE/NDT in industries like aerospace and robotics, improving reliability and productivity.
The future of NDE/NDT lies in integrating AI, Robotics, and IoT. AI enables accurate predictions and timely maintenance, while Robotics and digital twin technology facilitate precise replication and simulation. IoT enhances interoperability and real-time monitoring.
Continued research and development are crucial for overcoming industry challenges. Manufacturers should adopt a systematic approach to digital quality, setting clear objectives and implementing phased plans. The future of NDE/NDT lies in strategic integration, continuous improvement, and alignment with the evolving manufacturing and quality control landscape.