How to Conduct an Inspec Furniture Quality Inspection: A Step-by-Step Guide
Ensure top-quality inspec furniture with our step-by-step guide for effective quality inspections.
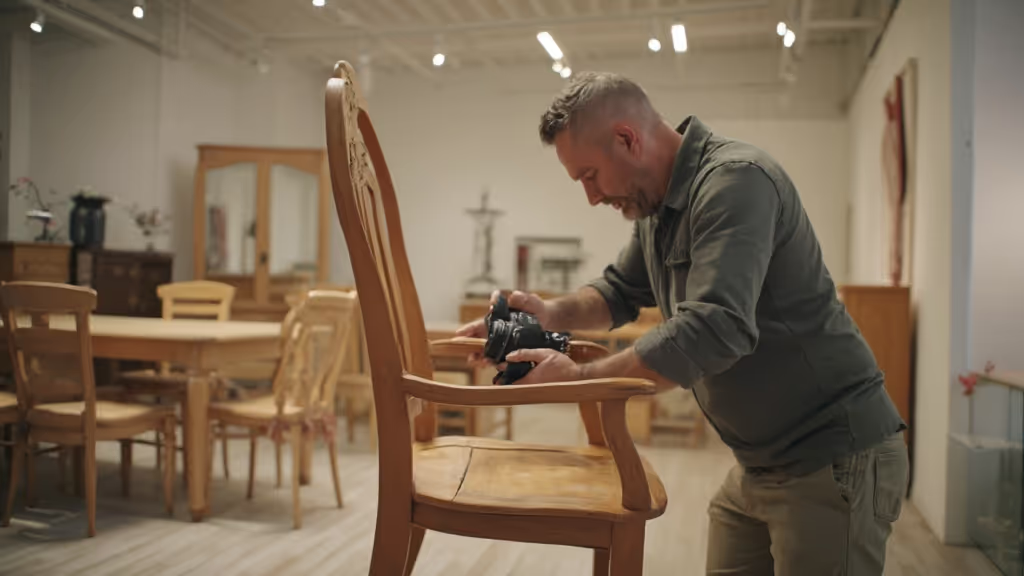
Overview:
The article provides a comprehensive step-by-step guide for conducting furniture quality inspections, emphasizing the importance of such evaluations in ensuring product excellence, durability, and safety. It supports this by detailing key processes, common defects to look for, and the benefits of inspections, such as enhanced customer satisfaction and reduced return rates, ultimately illustrating how structured inspections can significantly improve brand reputation and operational efficiency.
Key Highlights:
- Furniture quality inspections ensure compliance with standards of excellence, durability, and safety.
- Proactive evaluations help identify flaws early, reducing customer complaints and returns.
- Successful case studies illustrate the impact of inspections on revenue and customer trust.
- Key benefits include enhanced customer satisfaction, reduced return rates, and improved brand reputation.
- A structured inspection process involves preparation, visual checks, structural integrity assessments, and functional testing.
- Common defects include surface issues, structural weaknesses, material flaws, and functional failures.
- Implementing a quality control system involves defining standards, sourcing quality materials, and training teams.
- Continuous improvement relies on analyzing inspection data, establishing feedback loops, and incorporating customer feedback.
- Digital tools can enhance monitoring and reporting, leading to more efficient quality control processes.
Introduction
In the competitive landscape of furniture production, maintaining impeccable quality is not just a regulatory requirement but a cornerstone of brand loyalty and customer satisfaction. Quality inspections serve as a vital mechanism for ensuring that products meet established standards of durability, safety, and aesthetic appeal.
With a history steeped in quality assurance since 1984, organizations are increasingly recognizing the transformative impact of systematic inspections on their operations. From identifying defects early in the production cycle to enhancing customer trust, the benefits of a robust quality control system are manifold.
As industry leaders leverage data-driven insights and innovative inspection protocols, the path to operational excellence becomes clearer, ultimately safeguarding both brand reputation and consumer satisfaction.
This article delves into the essential aspects of furniture quality inspections, offering a comprehensive guide to best practices and highlighting the critical role these processes play in driving business success.
Understanding Furniture Quality Inspection: Importance and Benefits
Inspec furniture assessments are essential for ensuring that products conform to established standards of excellence, durability, and safety. Since 1984, quality assurance, supplier development, and factory consulting services have played a vital role in assisting companies in upholding these standards. By executing organized evaluations, companies can proactively recognize flaws early in the production cycle, significantly lowering the chances of customer grievances and returns.
This proactive methodology not only protects the reputation of the company but also fosters customer trust and loyalty. For example, OpsNinja's thorough evaluations assisted Amazon seller Maurice Mann in reclaiming $1 million in revenue by enhancing item ratings from 3.5 to 4.7 stars, showcasing the transformative effect of dependable assessment services on D2C enterprises. Moreover, Neil Ayton's effective management of various suppliers demonstrates how efficient control processes can optimize operations and improve offerings across multiple brands, including Caddent Golf and Karma Heart.
Creating a strong evaluation procedure improves operational efficiency by enabling the resolution of problems before items reach the market. As Soren Kaplan, Co-Founder of upBOARD, aptly states, "Digitize your manufacturing process 10x faster at one-tenth the cost," emphasizing the potential for improved efficiency through contemporary standards alongside comprehensive evaluations. Additionally, customer testimonials, such as those from Kari Fineran, highlight the effectiveness of OpsNinja's inspections in uncovering supplier discrepancies, like sizing issues, which can have substantial implications for merchandise standards and customer satisfaction.
Key Benefits of Furniture Quality Inspections:
- Enhanced Customer Satisfaction: Delivering high-quality products fosters positive customer experiences, which is essential in today's competitive market.
- Reduced Return Rates: Early detection of defects minimizes returns, subsequently lowering associated costs and improving profitability.
- Brand Reputation Management: Consistency in standards is vital for building and maintaining a favorable brand image, crucial for long-term success.
- Operational Efficiency: Streamlining evaluation processes can lead to significant cost savings and improved productivity. For instance, a furniture firm that employed data analytics not only discovered and resolved bottlenecks in their manufacturing process but also enhanced their inspec furniture protocols. By tackling these inefficiencies, the company significantly enhanced production speed while minimizing waste, illustrating the direct relationship between efficient assessments and overall operational success.
In summary, evaluations go beyond simple regulatory adherence; they symbolize a strategic investment in the brand's lasting success and customer satisfaction.
Step-by-Step Guide to Conducting a Furniture Quality Inspection
Carrying out an inspection furniture quality evaluation is essential for ensuring that products meet the highest standards of excellence. The following step-by-step guide will help facilitate effective evaluations:
-
Prepare Your Tools and Materials: Begin by gathering essential inspection tools, including a measuring tape, level, flashlight, and an inspection checklist. The right tools not only streamline the process but also enhance the accuracy of your evaluations.
-
Review the Specifications: Familiarize yourself with the product specifications and pertinent standards, including dimensions, materials, and weight limits that the furniture must adhere to, ensuring compliance with industry regulations.
-
Visual Inspection: Conduct a thorough visual assessment of the furniture. Look for visible defects such as scratches, dents, or inconsistencies in color. Additionally, check for proper assembly and alignment of parts, as these aspects are critical for both aesthetic appeal and functionality.
-
Structural Integrity Check: Evaluate the structural components by applying pressure to joints and connections to verify their stability and durability. For items such as chairs and tables, assess for wobbling or any signs of instability, which could compromise safety and usability.
-
Functional Testing: Test all moving parts, including drawers and hinges, to confirm they operate smoothly. Ensure that all features work as intended, paying particular attention to any adjustable components that may require fine-tuning.
-
Material Quality Assessment: Scrutinize the materials used in the furniture. Fabrics should be free from defects, while wood or metal components must meet established standards. Seek certifications that confirm the material standard, boosting consumer confidence in your products.
-
Documentation: Meticulously record your findings on the checklist, noting any defects or areas needing attention. This documentation is essential for standard assurance and future reference, and it should include a detailed report with photos and videos to provide a clear overview of the assessment process.
- Reporting Issues: If any defects are identified, promptly report them to the relevant stakeholders, such as manufacturers or suppliers. Ensure that corrective measures are implemented to resolve problems before items are sent to clients.
By following these steps, you can perform a comprehensive furniture evaluation that not only maintains your brand's dedication to excellence but also allows you to inspect furniture in accordance with the latest standards and best practices in the sector. Grasping AQL figures is essential in this process; the Accept Point for assessments stands at 12, indicating the maximum number of flaws allowable in a sample before an order can be approved based on Acceptable Quality Limit (AQL) standards. This is especially significant when examining the AQL chart overview, which details the sample size and permissible number of defective units for effective control.
Such strict evaluation procedures can positively influence your brand's reputation and customer satisfaction, ultimately shielding you from negative feedback and ensuring a high-quality delivery.
Common Defects to Look For During Inspections
Effective assessments to inspect furniture rely on recognizing typical flaws that can greatly affect item standards and customer satisfaction. Since 1984, assurance, supplier development, and factory consulting services have been essential in maintaining high standards in inspect furniture production. OpsNinja improves this process by offering on-site evaluations that prevent product returns and safeguard brand reputation.
Significantly, 60% of returns are attributed to avoidable problems, highlighting the necessity of these evaluations. The following are typical issues to be vigilant for:
- Surface Defects: Scratches, dents, and discoloration can undermine the aesthetic appeal of furniture, leading to customer disappointment. Studies show that roughly 30% of furniture returns result from surface defects, which OpsNinja assists in identifying early through thorough evaluations.
- Structural Issues: Weak joints, loose screws, and improper assembly can compromise stability and pose safety risks. A case study titled "Common Defects Found During Furniture Inspections" reveals that nearly 25% of inspect furniture had structural issues that could lead to safety hazards; OpsNinja’s thorough checks address these concerns effectively.
- Material Defects: Inspect upholstery for tears, fraying, or discoloration, and examine wooden components for knots or warping that could affect durability. Statistics indicate that approximately 15% of material defects occur due to inadequate control during production, which OpsNinja’s inspections aim to reduce.
- Finish Problems: Uneven staining, bubbling, or peeling paint may indicate subpar craftsmanship. Reports suggest that finish problems account for about 20% of consumer complaints; OpsNinja ensures that finishing processes are evaluated thoroughly.
- Functional Failures: All moving parts, such as drawers and hinges, should be tested for proper functionality. Issues like sticking drawers or squeaky hinges could signal underlying problems that need addressing, and OpsNinja inspects these components to ensure reliability.
Additionally, OpsNinja helps catch missing units, alerting you to discrepancies between ordered and received quantities, which is crucial for maintaining inventory accuracy.
By maintaining vigilance regarding these common defects, you can ensure that only inspect furniture of high quality reaches the market. This commitment not only enhances customer satisfaction but also bolsters your brand's reputation. As observed by inspection experts, understanding the Acceptance Quality Limit (AQL) is essential, as it sets standards that prevent defects from recurring.
In 2024, concentrating on these factors will be crucial, particularly as shown by how OpsNinja assisted Amazon seller Maurice Mann in regaining $1 million in revenue by improving item ratings from 3.5 to 4.7 stars through better oversight. Recent studies emphasize persistent difficulties in furniture standards, stressing the necessity for strong evaluation procedures to ensure consumer safety and satisfaction. With OpsNinja, you can enjoy peace of mind, knowing that your products are thoroughly inspected and your brand reputation is protected.
Implementing a Quality Control System for Furniture Inspections
Establishing a structured assurance control system is crucial for enhancing the effectiveness of inspec furniture inspections. Here’s a comprehensive approach to setting one up:
-
Define Standards: Begin by establishing clear performance benchmarks that not only align with customer expectations but also comply with industry regulations. This foundational step is vital for guiding all subsequent assurance efforts.
-
Sourcing Superior Materials: A key aspect of quality control is ensuring that the materials used in furniture production are of high caliber. By sourcing quality materials, manufacturers can significantly reduce the risk of defects and enhance the overall product quality.
-
Create a Review Protocol: Develop a standardized assessment checklist tailored to specific furniture types and common defects. A consistent review process helps ensure thorough evaluations, minimizing the potential for oversight. OpsNinja’s dedicated support team plays a crucial role here, enabling brands to catch issues early and prevent returns, as 60% of returns stem from avoidable problems. Ops Ninja provides different kinds of assessments, including pre-production reviews, in-process evaluations, and final product analysis, ensuring thorough coverage of assurance standards.
-
Train Your Team: Invest in proper training for all team members involved in the evaluation process. Acquaintance with standards and assessment methods is crucial, and regular training sessions will strengthen best practices and keep everyone informed about the latest requirements.
-
Utilize Technology: Embrace digital tools and platforms to monitor results and manage control processes effectively. Software solutions can streamline documentation and enhance reporting, making it easier to maintain high standards.
-
Conduct Regular Reviews: Schedule periodic evaluations of the control system to identify opportunities for improvement. Collecting feedback from inspectors and modifying protocols accordingly will help improve the evaluation process continuously.
-
Engage Suppliers: Collaborate closely with suppliers to ensure they are aware of and can meet your standards. Open lines of communication can help preempt issues before they reach the inspection phase, fostering a culture of excellence from the outset.
As J. Juran states in his quality-control handbook, "Quality is not an accident; it is the result of intelligent effort." By establishing this strong assurance system, furniture manufacturers can guarantee their items consistently adhere to high standards, leading to enhanced customer satisfaction and a decrease in returns when customers inspect furniture. This proactive method not only improves product standards but also strengthens company integrity in a competitive market.
Moreover, establishing guidelines to inspec furniture production is essential for ensuring that the furniture is safe, aesthetically pleasing, and structurally sound. Proper guidelines help manufacturers produce high-quality furniture that meets consumer expectations and regulatory requirements.
With OpsNinja as a reliable ally for assurance, companies can improve their reputation and dependability in the supply chain. According to a recent client testimonial, "Since partnering with OpsNinja, our return rates have decreased by 30%, and our customer satisfaction ratings have never been higher." This demonstrates the tangible effect of OpsNinja's services on control and customer satisfaction.
Continuous Improvement: Learning from Inspection Results
To foster a culture of ongoing enhancement, brands must leverage insights from their evaluation outcomes, as shown by successful D2C brands utilizing OpsNinja's services. Implementing the following strategies can significantly enhance product quality:
-
Analyze Inspection Data: Regularly scrutinize inspection findings to uncover trends and recurring issues. This data-driven approach not only informs design but also optimizes manufacturing processes. Recent advancements in AI highlight its capability to analyze production data, identifying inefficiencies and predicting demand for inventory management. For instance, data analytics can help manufacturers predict demand trends, optimize inventory levels, and identify potential disruptions in the supply chain, ensuring a smoother operational flow. Success narratives from firms like Hash Stash demonstrate how utilizing thorough evaluations resulted in more efficient operations and enhanced output.
-
Feedback Loop: Establish a robust feedback loop where inspectors communicate their insights with development teams. Such collaboration can result in innovative solutions that improve product quality and design, as demonstrated in testimonials where brands valued OpsNinja’s comprehensive evaluation process, which included detailed reports and actionable recommendations. Matthew Scullion remarked, "Prompt service, assessment covered in great detail including videos and lots of pictures. Great recommendations."
-
Benchmarking: Regularly compare your inspection results against industry standards and those of competitors. This practice enables brands to pinpoint areas for improvement and maintain a competitive edge, as emphasized in the report on emerging technologies shaping the inspec furniture market, which discusses how R&D activities are driving innovation in the sector.
-
Customer Feedback: Incorporate customer feedback into the enhancement process. Understanding customer experiences and expectations can reveal critical areas needing attention, thereby driving design changes that resonate with consumer preferences. The Mindful Collective initially hesitated to invest in inspections but discovered that OpsNinja changed their approach to control, facilitating their growth on Amazon.
-
Set Improvement Goals: Based on the insights gained, establish specific, measurable goals for enhancement. This structured approach allows for tracking progress and adjusting strategies as necessary.
By adopting a mindset of continuous enhancement and learning from customer success narratives, brands can significantly elevate their product standards, ultimately fostering greater customer satisfaction and loyalty. As Soren Kaplan noted, "Digitize your manufacturing process 10x faster at one-tenth the cost." This efficiency underscores the importance of digital transformation in adapting to consumer demands and enhancing overall quality.
Conclusion
Implementing effective furniture quality inspections is paramount for ensuring product excellence and customer satisfaction. The article highlights the critical role of systematic inspections in identifying defects early, which not only protects brand reputation but also fosters customer trust. By adhering to established quality standards, companies can significantly reduce return rates and enhance operational efficiency, ultimately leading to increased profitability.
The step-by-step guide provided serves as a valuable resource for conducting thorough inspections, emphasizing the importance of preparation and attention to detail. Identifying common defects—ranging from surface imperfections to structural issues—can prevent costly returns and enhance the overall quality of the furniture produced. Additionally, implementing a robust quality control system enables brands to streamline their processes and maintain high standards consistently.
Continuous improvement is essential in the pursuit of excellence. By analyzing inspection data, fostering a feedback loop between inspectors and product development teams, and integrating customer insights, brands can enhance their offerings and adapt to market demands. The commitment to quality not only safeguards consumer satisfaction but also strengthens brand loyalty in a competitive landscape.
In conclusion, furniture quality inspections are not merely a regulatory obligation; they represent a strategic investment in a brand's future. By prioritizing these inspections and embracing a culture of continuous improvement, companies can ensure their products meet the highest standards, thereby securing lasting success in the marketplace.