How to Conduct an LVD Test: A Step-by-Step Guide for Compliance
Learn the essential steps to conduct an LVD test for compliance and ensure product safety.
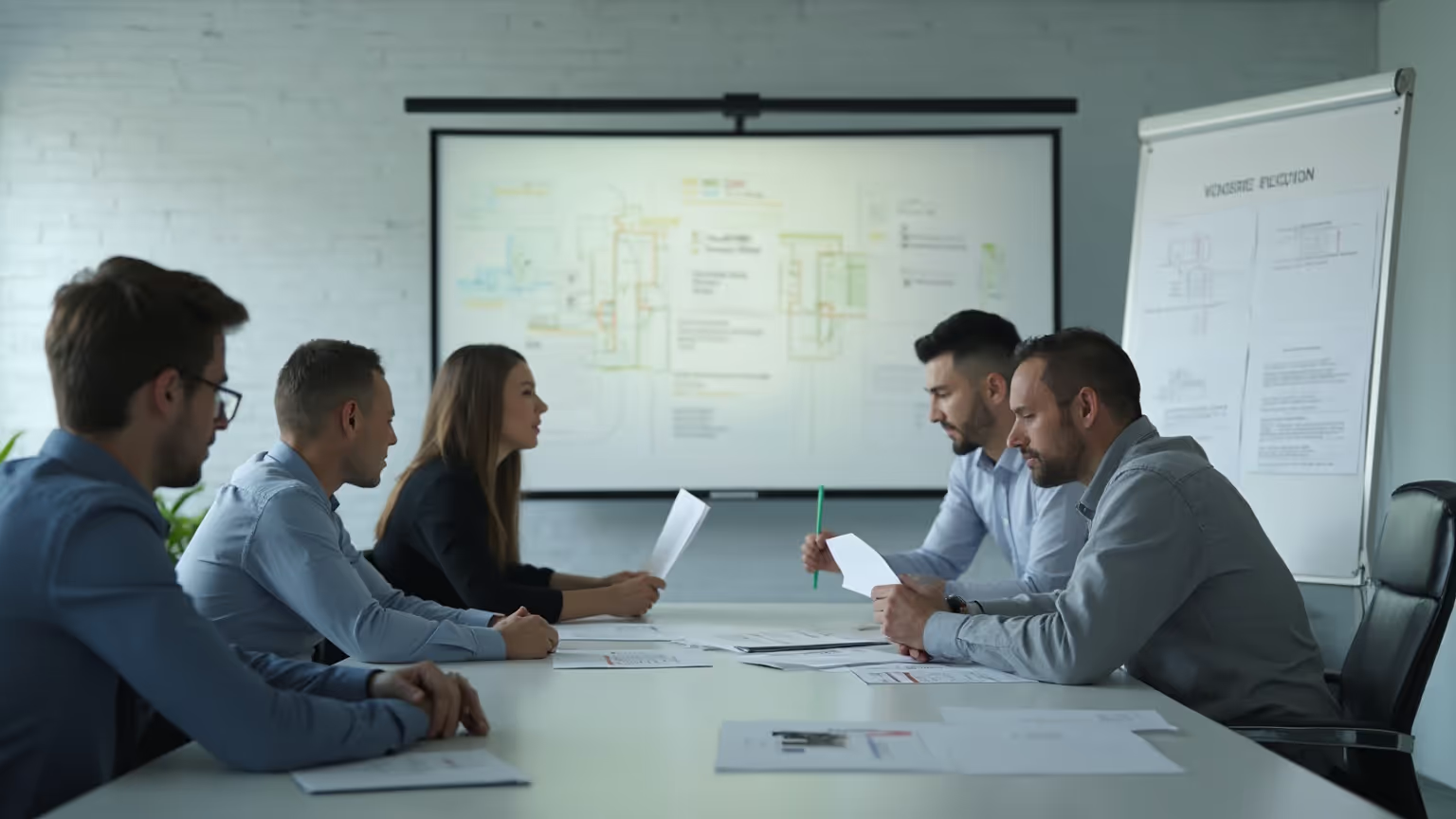
Overview:
To conduct an LVD test for compliance, manufacturers must follow a structured process that includes identifying applicable standards, performing risk assessments, and attaching the CE mark to their products. The article outlines these steps and emphasizes the importance of continuous monitoring and adaptation to regulatory changes to ensure ongoing compliance and enhance product safety, thereby protecting consumer trust and brand reputation.
Key Highlights:
- The Low Voltage Directive (LVD) is a key EU regulation ensuring electrical equipment within certain voltage limits meets safety standards.
- Products covered by the LVD include household appliances, power tools, and lighting systems.
- Compliance with the LVD enhances product safety, boosts consumer confidence, and protects brand reputation.
- Non-compliance can result in severe penalties, recalls, and reputational damage.
- Manufacturers must stay updated on LVD and related EU regulations for ongoing compliance.
- Steps for achieving LVD compliance include identifying applicable standards, conducting risk assessments, and attaching the CE mark.
- Common challenges in LVD compliance include inadequate understanding of standards, evaluation failures, documentation gaps, and costs.
- Best practices for continuous improvement post-compliance include regular audits, feedback systems, ongoing training, and leveraging technology.
- Staying informed about regulatory changes is crucial for maintaining compliance and adapting strategies accordingly.
Introduction
The Low Voltage Directive (LVD) stands as a cornerstone of electrical safety within the European Union, ensuring that a wide range of electrical equipment meets rigorous safety standards. As manufacturers navigate the complexities of compliance, understanding the LVD's implications is paramount—not only for regulatory adherence but also for fostering consumer trust and safeguarding brand integrity.
This article delves into the critical aspects of the LVD, outlining its significance, the step-by-step process for achieving compliance, and the common challenges faced by manufacturers. Additionally, it highlights best practices for maintaining compliance in a rapidly evolving regulatory landscape. By equipping organizations with the knowledge to navigate these requirements, this guide serves as a valuable resource for those committed to enhancing product safety and operational excellence.
Understanding the Low Voltage Directive (LVD): Importance and Scope
The Low Voltage Directive (LVD) includes the lvd test, which is an essential European Union regulation created to ensure that electrical equipment functioning within certain voltage limits meets rigorous standards, thus protecting human health and well-being. This directive encompasses a broad range of items, including household appliances, power tools, and lighting systems, making it essential for manufacturers to fully understand its scope. Adherence to the lvd test is not just a regulatory obligation; it fundamentally improves item security, fosters consumer confidence, and strengthens brand reputation.
Notably, statistics indicate that the electrical safety of cord extension sets has shown significant improvement in compliance, underscoring the importance of adherence to the lvd test. The consequences of non-compliance can be severe, leading to substantial penalties, recalls, and damage to a company's reputation. As the European market continues to evolve, manufacturers must stay informed about updates to the lvd test and other relevant EU regulations, such as the newly harmonized standards for fertilizing materials (EN 17816, EN 17817, EN 12580, EN 15560, and EN 12946).
Moreover, it is essential for manufacturers to evaluate the adherence of CE marked components when they are integrated into completed items, as emphasized by Sicom Test:
'The EMC Directive pertains to any finished device, or combination of finished devices, made available on the market as an independent functional unit, intended for the end user and capable of generating electromagnetic disturbances, or whose operation may be affected by such disturbances.'
This perspective highlights the interconnected nature of compliance regulations and the necessity for manufacturers to ensure that all components, especially those that may affect electromagnetic compatibility (EMC), are evaluated for compliance before being assembled into final items.
Step-by-Step Process for Achieving LVD Compliance
-
Identify Applicable Standards: Start by pinpointing the specific standards related to the lvd test that are relevant to your item. For instance, EN 60335 pertains to household appliances, while EN 60950 is applicable for IT equipment. Additionally, consider EN 61204, which specifies performance characteristics and requirements for low-voltage power supply devices. Each standard has distinct evaluation criteria that must be fulfilled to ensure compliance with the lvd test.
-
Conduct Risk Assessment: A thorough risk assessment is essential to identify potential hazards associated with the item. This evaluation is essential for establishing the necessary protection measures and testing protocols. It's important to note that, as highlighted by Sicom Test, the general safety and electromagnetic compatibility directives must apply to the item in question. Compliance with these directives must be verified on the finished item to ensure market readiness in Europe.
-
Choose a Notified Body: If your item falls into specific categories, involving a Notified Body for evaluation and certification may be necessary. Select a Notified Body that specializes in your category and has a strong reputation for quality and reliability.
-
Perform LVD Test: Execute the required assessment in accordance with the applicable standards. This process may involve various assessments, including electrical safety tests, thermal tests, mechanical tests, and the lvd test, to ensure compliance with established safety requirements. Maintaining item quality through comprehensive examination is essential for D2C brands striving to preserve their reputation.
-
Compile Technical Documentation: Record all testing results, risk assessments, and regulatory measures undertaken. This technical documentation is crucial for showing conformity during audits or inspections, acting as a record of your item’s adherence to regulatory standards.
-
Attach the CE Mark: After attaining adherence, attach the CE mark to your item, indicating that it fulfills all EU standards. Ensure the item is accompanied by a Declaration of Conformity to provide further assurance of compliance.
-
Track and Uphold Standards: Once adherence is achieved, it's essential to frequently observe your item's performance and security. Stay informed about any changes in regulations or standards that may affect your adherence status. Performing regular audits and evaluations will assist in maintaining continuous adherence, ensuring your item continues to meet essential safety benchmarks.
Consequences of Non-Adherence: Failing to meet these standards can lead to significant penalties, including fines, recalls, and harm to your brand’s reputation. Thus, following regulatory assessments is not just a legal requirement but also an essential element of preserving customer trust and satisfaction.
Case Study Example: A practical illustration of the LVD test applicability can be seen in the evaluation of a home exercise bike that generates its own power. If the voltages generated by the bike are under 50 volts, the LVD does not apply; instead, the General Product Safety Directive must be followed, highlighting the significance of understanding product specifications in regulatory processes.
Recent Updates: Staying informed about the latest news concerning adherence procedures is essential. For instance, the ISED issued an RSS update on December 24, 2024, highlighting significant changes that may impact your adherence strategy. By prioritizing adherence testing, D2C brands like yours can prevent returns and stop bad reviews, ensuring long-term success and customer satisfaction.
With OpsNinja, you can achieve peace of mind knowing that your products meet all necessary requirements, allowing your team to focus on growth rather than operational issues.
Common Challenges in LVD Compliance and How to Overcome Them
-
Inadequate Understanding of Standards: The intricacies of Low Voltage Directive (LVD) standards can be a significant hurdle for many manufacturers. To address this challenge, it is crucial to invest in comprehensive training and education for your team. Engaging with industry experts can further clarify specific requirements and enhance your team's understanding of compliance mandates. As seen in healthcare, an interprofessional approach has decreased heart-failure related hospital admissions by 27% and all-cause mortality by around 25%, illustrating the power of structured education and collaboration.
-
Evaluation Failures: Initial evaluation failures often stem from non-compliance with safety standards. To mitigate this risk, consider implementing pre-compliance evaluation. Leveraging internal assets or partnering with external laboratories can offer valuable insights and pinpoint potential problems prior to official evaluations, thus facilitating a smoother route to adherence. As emphasized by Nurse Assist, LLC, when the recall was first issued in November 2023, no negative effects had been reported, highlighting the significance of thorough testing and adherence. Furthermore, grasping the Process Capability Index (CPK), a statistical indicator of how effectively a process can generate output within defined limits, can assist in assessing how well your processes are performing against the requirements, thus lowering the chances of failures in testing.
-
Documentation Gaps: A typical issue manufacturers encounter is the existence of incomplete or poorly organized documentation, which can greatly hinder regulatory efforts. Establishing a structured documentation process early in the product development phase is essential. This ensures that all necessary records are meticulously maintained, facilitating a more efficient regulatory journey. The systematic review on interprofessional approaches in heart failure management shows that organized strategies can lead to improved outcomes, a principle that can be applied to the LVD test adherence as well. Additionally, leveraging CPK can help ensure that your documentation reflects a process that's capable of producing quality outputs consistently, which is crucial for demonstrating compliance.
-
Cost of Adhering to Standards: The financial implications of meeting regulatory standards can be daunting for many organizations. To mitigate this burden, it is advisable to budget for compliance-related costs from the outset of product development. Furthermore, investigating grants or funding options designed for your sector can reduce some financial strain and assist your regulatory efforts. By optimizing your processes with an emphasis on CPK, which quantitatively assesses process capability, you may also discover efficiencies that can lower regulatory costs over time.
-
Keeping Up with Regulatory Changes: Regulatory landscapes are constantly evolving, which can lead to unforeseen non-compliance scenarios. To remain informed about changes in LVD regulations, consider subscribing to industry newsletters, attending relevant conferences, and engaging with professional organizations. Staying updated will empower your organization to adapt promptly and effectively to any regulatory shifts, while also ensuring that your processes are capable, as indicated by CPK assessments.
Post-Compliance: Best Practices for Continuous Improvement
-
Regular Audits and Reviews: Establishing a timetable for routine audits of adherence processes and performance of goods is essential. These audits serve to identify potential areas for improvement, allowing for the proactive resolution of issues before they escalate into significant problems. As emphasizes, "Compliance review and monitoring are vital; companies must regularly assess their systems to ensure adherence to relevant regulations, including the Low Voltage Directive (LVD)." Additionally, manufacturers must maintain accurate and up-to-date records related to the design, production, testing, and adherence of the device for traceability.
-
Feedback Loop: Creating a strong feedback system with clients and stakeholders is essential for obtaining insights on performance and security. This feedback can influence product development and direct regulatory strategies, improving overall security and satisfaction levels.
-
Invest in Training: Ongoing education on regulations and protective practices should be a priority for your team. Regular training sessions promote a culture of adherence and quality within the organization, significantly impacting success rates. Knowledgeable employees are better equipped to uphold safety protocols consistently.
-
Stay Updated: Keeping abreast of changes in the regulations related to the LVD test is a fundamental aspect of adhering to the rules. Frequent assessments of industry publications and involvement in pertinent workshops will guarantee that your adherence practices stay up-to-date and efficient, reducing the risk of non-adherence.
-
Leverage Technology: Utilizing digital tools and platforms for quality control and regulatory management can streamline processes significantly. These technologies enhance documentation accuracy and improve overall efficiency, making it easier to uphold standards with the LVD test and other regulations.
-
Case Study Insight: For instance, consider how OpsNinja has positively impacted hundreds of brands, including helping Maurice Mann improve his Amazon star ratings from 3.5 to 4.7, recovering $1 million in revenue by implementing effective quality control measures. Similarly, The Mindful Collective transformed their quality control approach with OpsNinja’s guidance, leading to growth on Amazon. These success stories emphasize the significance of regular inspections and quality management in preventing returns and improving brand reputation. Additionally, the case study involving Hash Stash and their 10,000 monthly inspections underscores how proactive quality control can mitigate risks and ensure compliance, particularly regarding misleading voluntary certificates that can mislead consumers about product compliance with EU regulations. Entrepreneur Neil Ayton also shares insights on managing diverse suppliers and establishing quality control processes, emphasizing the significance of these practices for e-commerce brands. To learn more about how OpsNinja has transformed quality control for various brands, explore our customer stories.
Conclusion
Understanding the Low Voltage Directive (LVD) is essential for manufacturers aiming to ensure the safety and compliance of their electrical products within the European Union. The LVD not only establishes stringent safety standards but also plays a crucial role in enhancing consumer trust and protecting brand reputation. By following a systematic approach to compliance—ranging from identifying applicable standards to conducting thorough testing and maintaining meticulous documentation—manufacturers can navigate the complexities of the directive effectively.
The challenges associated with achieving and maintaining LVD compliance, such as inadequate understanding of standards, testing failures, and documentation gaps, can be addressed through proactive strategies. Investing in training, implementing pre-compliance testing, and establishing structured documentation processes are vital steps in overcoming these hurdles. Moreover, staying informed about regulatory changes and budgeting for compliance-related costs can further support manufacturers in their compliance journey.
In a rapidly evolving regulatory landscape, continuous improvement is key. Regular audits, fostering a feedback loop, and leveraging technology can enhance compliance efforts and product safety. By prioritizing these best practices, organizations can not only meet the requirements of the LVD but also drive operational excellence and build lasting consumer confidence. Ultimately, a commitment to compliance is not just about adhering to regulations; it is about safeguarding public safety and positioning brands for long-term success in the marketplace.