Investigating the Checking Process: A Case Study in Quality Assurance
Explore the checking process in QA with case studies on improving product quality and customer satisfaction.
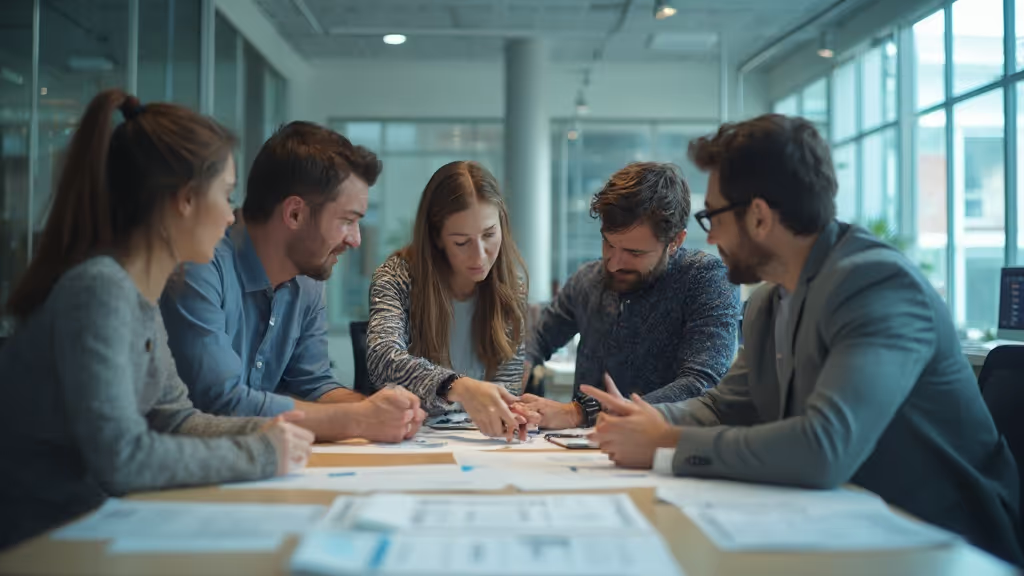
Introduction
Quality assurance and quality control are fundamental concepts in ensuring that products meet required standards and specifications. While quality assurance focuses on optimizing the processes and systems involved in product development, quality control deals with the operational activities that fulfill these quality requirements. This article explores these critical elements through a series of case studies and practical examples, illustrating their impact on various industries.
The journey of Martin Faist, Vice President of Quality Assurance at Absolute Hotel Services, showcases the transformative power of comprehensive QA measures. By streamlining brand standards and integrating QA across multiple departments, Martin significantly improved product reliability and compliance within the organization. Similarly, an electronics manufacturer faced high return rates and customer dissatisfaction due to quality issues.
By adopting ISO-9001 standards and refining their QA processes, they achieved a notable reduction in return rates.
The article delves into the adoption of QA frameworks like Total Quality Management and Six Sigma, which provide structured approaches to continuous improvement and operational efficiency. However, implementing enhanced QA processes comes with challenges, such as staff resistance to change and the financial barriers of new systems. Overcoming these hurdles requires strong leadership and a commitment to fostering a quality-oriented culture.
Finally, the article outlines best practices for effective quality assurance, emphasizing the importance of clear quality objectives, ongoing staff training, open communication with suppliers, and regular updates to QA processes. These strategies ensure that products not only meet but exceed market demands, thereby enhancing customer satisfaction and maintaining competitive advantage.
Understanding Quality Assurance and Quality Control
Quality assurance (QA) and quality control (QC) are crucial for confirming that items satisfy necessary standards and specifications. QA focuses on the processes and systems that lead to product development, aiming to improve and stabilize production and associated processes. On the other hand, QC encompasses the operational methods and tasks employed to meet standards.
An enlightening case study involves Martin Faist, Vice President of Quality Assurance at Absolute Hotel Services (AHS). With a career spanning Michelin-starred kitchens to his current role, Martin has consistently aimed to elevate service quality. At AHS, he implemented comprehensive QA measures, starting with streamlining food and beverage brand standards and evolving to encompass broader departments such as Front Office, Housekeeping, and Engineering. This holistic approach has significantly improved the reliability and compliance of offerings within the company.
Martin's journey highlights that assurance of standards goes beyond adherence to provide exceptional, dependable offerings and services. His strategic efforts exemplify how QA can be systematically integrated across various departments, ensuring consistent and positive outcomes.
Case Study: Evaluating Quality Assurance Processes
An electronics producer struggled with elevated return rates and customer discontent due to issues with standards. To address these challenges, the company embarked on a comprehensive evaluation of its quality assurance (QA) processes. This assessment uncovered significant gaps in supplier verification and testing protocols. To mitigate these issues, the company adopted the ISO-9001 standard, which emphasizes continuous improvement through the Plan-Do-Check-Act (PDCA) cycle. By applying a more stringent vendor selection method, carrying out regular evaluations, and improving item testing protocols, the company realized a 30% decrease in return rates within six months. This demonstrates the essential significance of enhancing QA processes to maintain product standards and fulfill customer expectations.
Quality Assurance Frameworks and Tools
To enhance their assurance efforts, the manufacturer adopted multiple QA frameworks, notably Total Management (TQM) and Six Sigma. These methodologies offered a structured approach to continuous enhancement and management, improving operational efficiency. By integrating specialized software tools for tracking performance metrics and automating reporting, the company could monitor compliance standards more effectively. This alignment of frameworks and tools established a robust culture of quality throughout the organization, much like how Absolute Hotel Services has maintained service excellence through meticulous attention to quality across departments. This strategic method is also evident in Hitachi's use of cutting-edge IT products and services to optimize business operations, leading to improved productivity and a greater return on investment (ROI).
Challenges in Implementing Quality Assurance
'Despite achieving positive outcomes, the organization encountered significant hurdles while implementing enhanced QA methods.'. Resistance to change among staff was a notable issue, as employees were accustomed to existing workflows and hesitant to adapt to new methodologies. Insufficient training on the newly introduced systems further compounded the problem, highlighting a critical need for comprehensive training programs to ensure smooth transitions. Additionally, the initial costs associated with implementing these processes presented a substantial financial barrier.
Collaborating with vendors to achieve new criteria also required significant effort. This was particularly challenging in a competitive and rapidly innovating sector where supply chain visibility is crucial. As mentioned by GOCOMET, supply chain visibility entails tracking and monitoring products and materials in real-time, ensuring all components meet strict standards. Manufacturers must manage global logistics operations and mitigate risks of supplier dependency, all while keeping pace with demand.
Addressing these challenges required strong leadership and a commitment to fostering a quality-oriented culture within the organization. Leaders needed to emphasize the significance of management systems, which, as defined, are formal sets of policies, processes, and procedures established to elevate consumer satisfaction. This cultural shift was essential to overcoming resistance and ensuring consistent adherence to new standards.
Best Practices for Effective Quality Assurance
Effective assurance (QA) is integral for maintaining high standards and ensuring customer satisfaction. Setting clear standards for excellence aligned with customer expectations is essential. This alignment not only establishes the standard for excellence but also guarantees that the products satisfy market requirements.
Ongoing training and development for staff on QA principles are crucial. It equips employees with the necessary skills and knowledge to maintain high-quality standards consistently. As emphasized by the National Academies of Sciences, Engineering, and Medicine, ongoing education promotes a setting where scientific and engineering principles are utilized to enhance standards and efficiency.
Keeping transparent dialogue with suppliers regarding standards encourages teamwork and reliability. This approach is reflected in the wind energy sector, where manufacturers must ensure that all turbine components meet strict standards to deliver dependable performance. Engaging in discussions with suppliers aids in reducing risks linked to supply chain challenges and guarantees that the final outcome meets the expected standards.
Consistently evaluating and revising quality assurance methods based on performance information and input can greatly improve the quality of items over time. This repetitive method enables the discovery and correction of flaws early in the production cycle, lowering expenses and enhancing overall reliability. The World Quality Report emphasizes the importance of incorporating performance data to drive ongoing improvements in QA processes, ensuring products remain competitive and meet evolving customer expectations.
Conclusion
Quality assurance and quality control are pivotal in ensuring that products not only meet but exceed required standards and specifications. Through the case studies presented, such as the transformative journey of Martin Faist at Absolute Hotel Services and the challenges faced by an electronics manufacturer, it is clear that implementing robust QA processes is essential for enhancing product reliability and customer satisfaction. The adoption of frameworks like Total Quality Management and Six Sigma provides structured approaches to continuous improvement, ultimately driving operational efficiency across various sectors.
However, the path to effective quality assurance is not without its challenges. Resistance to change, financial constraints, and the necessity for comprehensive training are hurdles that organizations must navigate to foster a quality-oriented culture. Strong leadership and a commitment to quality management systems play a critical role in overcoming these obstacles, ensuring that employees are equipped and motivated to embrace new methodologies.
Best practices, such as establishing clear quality objectives, ongoing staff development, and maintaining open communication with suppliers, are fundamental to achieving lasting improvements in quality assurance. Regularly reviewing and updating QA processes based on performance data further enhances product quality and operational resilience. By prioritizing these strategies, organizations can not only meet market demands but also maintain a competitive edge, ultimately leading to increased customer satisfaction and loyalty.