Understanding NCR Non Conformance: A Complete Tutorial for Quality Management
Explore NCR non-conformance for effective quality management and improved customer satisfaction.
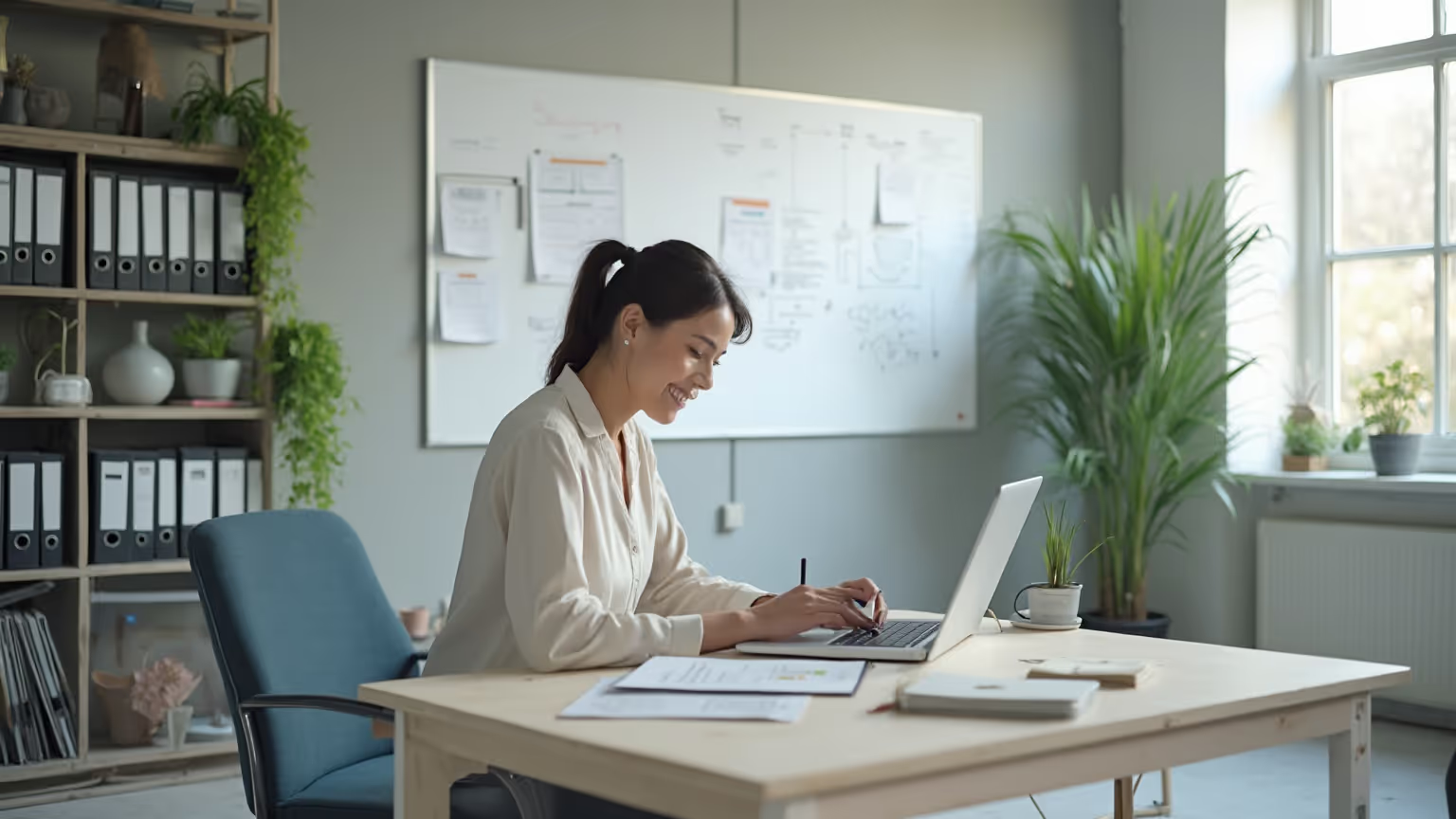
Overview:
Understanding NCR non-conformance is essential for effective quality management, as it involves identifying deviations from established standards and implementing corrective actions to enhance operational efficiency and customer satisfaction. The article emphasizes that a structured approach to managing Non-Conformance Reports (NCRs), including defining issues, documenting evidence, and fostering a culture of continuous improvement, can lead to significant reductions in customer complaints and improvements in product quality, as illustrated by the case of Hash Stash.
Key Highlights:
- Non-Conformance Reports (NCRs) identify deviations from standards, crucial for quality assurance.
- Hash Stash experienced a 30% reduction in customer complaints after implementing NCR management strategies.
- Addressing NCR non-conformance is vital for enhancing operational efficiency and customer satisfaction.
- The NCR lifecycle includes identifying issues, investigating causes, and implementing corrective actions.
- Common causes of NCR non-conformance include poor communication, inadequate training, and resource shortages.
- Effective NCR management involves defining non-conformance, documenting evidence, assigning responsibility, and following up on corrective actions.
- NCRs contribute to continuous improvement by identifying systematic issues, benchmarking performance, and fostering a quality culture.
- Best practices for NCR management include standardizing templates, training employees, and leveraging technology for tracking and analysis.
Introduction
In the quest for operational excellence, Non-Conformance Reports (NCRs) emerge as vital instruments for organizations striving to uphold quality standards. These formal documents not only identify discrepancies in products or processes but also facilitate a structured approach to investigating root causes and implementing corrective actions.
For direct-to-consumer (D2C) brands, like Hash Stash, effective NCR management has proven to be a game-changer, significantly reducing customer complaints and enhancing brand reputation. As industries grapple with increasing compliance pressures and the need for continuous improvement, understanding the intricacies of NCRs becomes essential.
This article delves into the importance of NCRs, best practices for their management, and how they can serve as a cornerstone for fostering a culture of quality and operational efficiency.
Introduction to Non-Conformance Reports (NCRs)
Non-Conformance Reports (NCRs) are formal documents that play a crucial role in assurance by identifying and reporting instances of NCR non-conformance, where products or procedures deviate from established standards. These reports serve as essential tools for organizations, enabling them to document NCR non-conformance, investigate root causes, and implement corrective actions to prevent recurrence. For D2C brands such as Hash Stash, utilizing effective NCR non-conformance methods can significantly reduce negative reviews and customer complaints, ultimately safeguarding brand reputation.
In a recent case study, Hash Stash reported a 30% decrease in customer complaints after adopting OpsNinja's approaches to address NCR non-conformance, demonstrating a direct connection between control standards and customer satisfaction. In industries such as manufacturing, healthcare, and services, addressing NCR non-conformance is indispensable for maintaining high-quality benchmarks. By acknowledging and addressing NCR non-conformance, organizations can enhance operational efficiency, minimize waste, and improve customer satisfaction.
The lifecycle of an NCR non-conformance—from the initial identification of an issue to its thorough resolution—is essential for effective process oversight. Recent findings indicate that 27% of security and IT professionals rank mitigating internal audit fatigue as a top compliance challenge, highlighting the broader compliance landscape that NCRs operate within. Furthermore, 40% of supply chain professionals view risk oversight and supply chain resilience as their main concern, emphasizing the need for strong NCR non-conformance processes to handle these compliance pressures.
Moreover, with 50% of organizations dedicating 6-10% of their revenue to compliance expenses, the strategic execution of NCR non-conformance emerges as a vital element in enhancing management and ensuring long-term organizational success. Additionally, the increasing emphasis on environmental, social, and governance (ESG) matters is evident in that 77% of corporate risk and compliance experts appreciate updates on ESG-related developments, highlighting the significance of NCRs in tackling changing compliance challenges and improving control for e-commerce brands. By effectively managing NCR non-conformance, brands can not only comply with regulations but also achieve significant operational efficiencies, as demonstrated by Hash Stash’s enhanced performance metrics post-implementation.
How to Write and Manage Non-Conformance Reports Effectively
To write and manage NCR non conformance reports effectively, adhere to these essential steps:
-
Define the Non-Conformance: Clearly articulate the issue at hand, providing specific details regarding the product or procedure that deviated from established standards. This precision is critical for effective resolution.
-
Document Evidence: Gather and attach supporting evidence, such as photographs, inspection reports, or measurements, to substantiate the NCR. Good Documentation Practices (GDPs) are vital; as emphasized in the pharmaceutical industry, if it’s not documented, it didn’t happen. This practice ensures that all relevant details are captured for future reference and compliance.
-
Assign Responsibility: Designate a responsible team member to investigate the non-conformance and oversee the implementation of the corrective action plan. Accountability is key to ensuring timely resolution.
-
Investigate Root Causes: Conduct a comprehensive analysis to uncover the root causes of the non-conformance.
Employ techniques such as the 5 Whys or Fishbone Diagram to facilitate this examination, as understanding the 'why' is crucial for effective problem-solving. -
Develop Corrective Actions: Outline specific, actionable steps that will address the non-conformance and prevent future occurrences. Ensure these actions are both realistic and time-bound, promoting accountability and focus.
-
Follow Up and Review: After implementing corrective actions, closely monitor their effectiveness. Schedule a review to confirm the issue has been resolved and document any lessons learned, fostering a culture of continuous improvement. Management reviews play a vital role in this process, helping to identify trends and areas for improvement in systems.
-
Maintain Records: Keep detailed records of all NCRs and associated documentation for future reference and compliance audits. This practice not only helps in recognizing trends and areas for enhancement but also reinforces the overall system of oversight.
-
Incorporate Customer Feedback: Systematically integrate customer feedback into the NCR management framework. This feedback is essential for identifying defects and shortcomings in products, enabling organizations to make informed decisions that align with market demands.
-
Understand AQL Numbers: AQL (Acceptable Quality Level) figures are essential for directing the inspection procedure. They establish the benchmark of acceptability for a product batch and assist in deciding how many items should be examined.
By incorporating AQL numbers into the NCR non conformance process, organizations can ensure that they uphold high standards while effectively addressing non-conformances.
By diligently following these steps, organizations can enhance their NCR processes, ultimately leading to improved product standards and greater customer satisfaction. As demonstrated by brands such as Maurice Mann's, which enhanced its rating from 3.5 to 4.7 stars and regained $1 million in revenue through effective control measures, a successful Quality Manager understands that an NCR non conformance report can simultaneously enhance product standards and increase the business's sustainability. Leveraging customer feedback also plays a pivotal role in identifying defects, which is essential for continuous product improvement.
Common Causes of Non-Conformance
Recognizing the shared reasons for ncr non conformance is vital for improving practices, particularly for D2C brands aiming to scale successfully. OpsNinja has positively impacted hundreds of brands by helping them scale and avoid negative customer reviews with our platform. Several key factors frequently contribute to this issue:
-
Poor Communication: Insufficient communication among teams frequently results in misunderstandings concerning expectations and standards. Significantly, 40% of supply chain experts mention risk management and supply chain resilience as their main issues, highlighting the essential role communication has in upholding standards. Furthermore, 67% of global executives find ESG regulation too complex, highlighting the need for clear communication in navigating compliance challenges.
-
Inadequate Training: Employees lacking proper training may fail to understand the importance of control or the necessary adherence to established standards. As organizations increasingly prioritize compliance, the effectiveness of training programs becomes paramount. In fact, 60% of risk and compliance professionals plan to include cybersecurity as a training topic in the next two to three years, indicating a proactive approach to enhancing compliance through education.
OpsNinja's leadership excellence, spearheaded by Sajag Agarwal, our CEO who founded a $2M/yr brand, ensures that training programs are robust and aligned with industry standards.
-
Lack of Resources: Insufficient tools, equipment, or materials can severely hinder employees' ability to meet quality requirements, further exacerbating issues related to ncr non conformance. By leveraging blockchain technology, OpsNinja enhances transparency and security, ensuring that resources are effectively managed throughout the supply chain.
-
Procedure Inefficiencies: Outdated or poorly designed methods create opportunities for errors, which can directly lead to ncr non conformance. Organizations must regularly assess and enhance their procedures to minimize these risks. OpsNinja offers comprehensive audits, including process evaluations, to identify and rectify inefficiencies.
-
Supplier Issues: Performance problems stemming from raw materials or components provided by third parties can significantly compromise the overall standard of the end product. With 35% of executives expressing concern over third-party breaches, it is essential to ensure supplier standards align with organizational expectations. OpsNinja's comprehensive background check audits ensure supplier credibility through business registration, qualifications, and legal compliance.
Moreover, 77% of corporate risk and compliance professionals value staying updated on the latest ESG-related developments, which underscores the significance of training and compliance in management. By recognizing these common causes of ncr non conformance, organizations can implement targeted strategies to mitigate risks. OpsNinja's expert inspections and dedication to assurance empower D2C brands to improve their management systems, ultimately reducing the occurrence of ncr non conformance and boosting ratings and revenue.
Under the guidance of our CTO Rafael Petry, who has extensive experience in technology within outdated industries, and Jake Corkin, our Head of Product with a strong background in home goods brands, OpsNinja continues to lead the way in transforming control for D2C brands.
Implementing Corrective Actions for NCRs
Implementing corrective actions in response to an NCR non conformance is essential for maintaining standards and fostering a culture of continuous improvement. OpsNinja's dedicated support team exemplifies this commitment, enhancing customer experience in supply chain oversight and ensuring impartial standards in inspections. This team offers a range of services, including detailed product inspections, compliance checks, and tailored quality management solutions aimed at identifying and resolving discrepancies in supplier quality.
A case study titled "A Culture of Quality" demonstrates how empowering employees to report issues confidently can enhance operational excellence. Here are the key steps to effectively address NCRs:
-
Prioritize Actions: Assess and prioritize the corrective actions that are critical for addressing the non-conformance and preventing its recurrence. Effective prioritization is vital for ensuring that resources are allocated to the most impactful areas.
-
Develop an Action Plan: Establish a comprehensive action plan that delineates specific steps, assigns responsibilities to relevant parties, and sets clear timelines for implementation. This structured approach facilitates accountability and clarity in the corrective procedure.
-
Communicate with Stakeholders: Ensure that all stakeholders are informed about the corrective actions and understand their roles in the implementation process. Transparent communication fosters collaboration and encourages a solutions-focused approach within the organization.
-
Implement Actions: Execute the action plan diligently while ensuring that sufficient resources are allocated. This step is crucial for addressing the identified non-conformities effectively. For instance, a Singapore-based service provider successfully transitioned from a manual management system to Effivity QMS Software, illustrating effective corrective action implementation. Furthermore, customer testimonials, including Kari Fineran's account where she mentioned, 'I valued how the team notified me about the discrepancies in sizing that my supplier had missed,' emphasize how OpsNinja's inspections uncovered supplier discrepancies, thereby improving product standards and customer satisfaction.
-
Monitor and Evaluate: Regularly monitor the effectiveness of the implemented actions and evaluate their impact on preventing recurrence. This ongoing assessment is vital for continuous improvement and for adapting strategies as necessary.
-
Document Changes: Keep thorough records of all changes made as a result of the corrective actions. This documentation not only serves as a reference for future evaluations but also fosters a culture of excellence where transparency is prioritized.
Additionally, it is important to note that Purchase Order closeouts can be deferred until all action items related to NCR non conformance are completed. By following these steps, organizations can effectively manage NCR non conformance, thereby reinforcing their commitment to excellence and continuous improvement. The integration of these practices ensures that the investigation of root causes is thoroughly conducted, ultimately leading to enhanced operational excellence.
The Role of NCRs in Continuous Improvement
NCR non conformance reports serve as a cornerstone in the continuous improvement cycle, offering various advantages to organizations committed to refining their process standards. For D2C brands like Hash Stash, which examines 10,000 units monthly, effective management of NCR non conformance, supported by OpsNinja's streamlined control and supplier management, can significantly enhance operational efficiency and drive revenue recovery. Here are the key roles NCRs play:
-
Identifying Systematic Issues: By meticulously analyzing NCR non conformance reports, organizations can uncover underlying patterns and trends that highlight systemic issues requiring intervention. This proactive approach not only resolves current problems but also prevents future occurrences, enabling brands to scale operations effectively.
-
Benchmarking Performance: NCR data offers valuable insights for benchmarking performance against industry standards and internal objectives. This practice fosters accountability and encourages organizations to strive for excellence, ensuring they remain competitive in their respective fields.
-
Fostering a Quality Culture: Documenting non-conformities promotes a culture of transparency within organizations, encouraging employees to report issues without fear. Actively addressing NCR non conformance enhances employee engagement and commitment to maintaining high-quality standards, ultimately creating a more cohesive and motivated workforce.
-
Driving Innovation: Insights gained from analyses of NCR non conformance can catalyze continuous improvement initiatives that lead to innovative solutions and enhancements. Organizations that embrace change driven by NCR findings are better positioned to adapt and thrive in an evolving market landscape.
-
Boosting Customer Contentment: The efficient handling of NCR non conformance directly influences the standard of products and services provided, resulting in greater customer satisfaction and loyalty. As organizations improve their systems based on NCR data, they establish a positive feedback loop that enhances the overall customer experience.
A real-world example of the role of technology in NCR oversight is illustrated by the use of Quality Management System (QMS) software, which OpsNinja employs to streamline inspections. Such software boosts the efficiency of oversight related to NCR non conformance, providing insights into performance issues and facilitating ongoing improvement. By utilizing technology, organizations can greatly enhance their control processes, as shown by Amazon seller Maurice Mann, who regained $1 million in revenue by elevating product ratings from 3.5 to 4.7 stars through effective inspections and oversight.
Incorporating NCR non conformance into the continuous improvement framework enables organizations to create a robust system aligned with their long-term objectives. As noted by Kaushal Sutaria, Managing Director at Effivity Technologies, "the dedication to best practices is crucial for organizations aiming for excellence in their operations." This commitment to best practices in managing NCR non conformance is essential for driving significant improvements that resonate across the entire operation.
Furthermore, OpsNinja utilizes specific methodologies in managing NCR non conformance, which involve regular audits and supplier evaluations to ensure compliance and standards are met, thereby safeguarding brands from negative reviews and improving customer experiences.
Best Practices for NCR Management
To optimize ncr non conformance management and protect your brand from negative reviews, consider the following best practices:
- Standardize NCR Templates: Implementing standardized templates for NCRs ensures consistency and completeness in reporting, which is critical for accurate data analysis and decision-making. Organizations adopting this approach have reported enhanced clarity in identifying non-conformance trends.
For example, as emphasized in numerous success narratives, including how Maurice Mann enhanced his Amazon star rating from 3.5 to 4.7, the implementation of standardized templates has resulted in substantial advancements in product excellence and customer satisfaction.
-
Train Employees: Regular training sessions for employees on the significance of NCRs and the correct procedures for completing them promote a culture of awareness. Skilled personnel are more inclined to identify and communicate non-conformances efficiently, promoting overall enhancements, as demonstrated in the evolution of control systems at The Mindful Collective.
-
Encourage Reporting: Creating an environment where employees feel empowered to report non-conformances without fear of repercussions is essential. This openness leads to greater reporting rates and, consequently, improved insights into quality control issues, which is vital for maintaining a strong brand reputation.
-
Leverage Technology: Embracing digital tools and platforms can significantly streamline the NCR procedure.
Technologies that automate tracking, management, and analysis of NCRs not only enhance efficiency but also provide valuable analytics that can guide future improvements. For example, OpsNinja's comprehensive inspection reports, which include photos and videos, deliver insights that safeguard your brand's reputation, demonstrating the practical application of technology in NCR management.
- Regularly Review Procedures: Conducting regular evaluations of NCR procedures allows organizations to identify areas for improvement and ensure they align with strategic goals.
This proactive approach not only improves the NCR workflow but also enables the organization to react swiftly to emerging challenges, as evidenced by Hash Stash's streamlined operations through effective control.
- Communicate Findings: Sharing insights from NCR analyses across the organization promotes transparency and collective learning. It enables all divisions to grasp the consequences of non-conformances and promotes a cohesive strategy for enhancement.
By adopting these best practices, organizations can greatly improve their processes related to ncr non conformance, resulting in better product standards, lower expenses, and increased customer satisfaction. The success stories of brands like Maurice Mann and Hash Stash demonstrate that effective NCR oversight is integral to achieving consistent quality standards and operational success, ultimately safeguarding your brand from negative reviews. Additionally, the detailed reports provided by OpsNinja not only help in acting on the results of NCR management but also serve as a crucial tool in safeguarding your brand's reputation.
Conclusion
Non-Conformance Reports (NCRs) are essential tools that facilitate organizations in their pursuit of quality assurance and operational excellence. By systematically identifying discrepancies, documenting evidence, and implementing corrective actions, brands can significantly enhance their quality management processes. The effective management of NCRs not only mitigates customer complaints but also fosters a culture of continuous improvement, as evidenced by the success stories of brands like Hash Stash and Maurice Mann.
Understanding the common causes of non-conformance is crucial for organizations aiming to enhance their quality practices. Issues such as:
- Poor communication
- Inadequate training
- Process inefficiencies
can lead to significant challenges. By addressing these underlying factors through targeted strategies, organizations can streamline their operations, improve product quality, and ultimately boost customer satisfaction.
Incorporating best practices in NCR management is vital for reinforcing a commitment to quality. Strategies such as:
- Standardizing templates
- Leveraging technology
- Encouraging employee reporting
create an environment conducive to effective quality control. As organizations adopt these strategies, they position themselves not only to comply with regulations but also to thrive in a competitive landscape.
In conclusion, the strategic implementation of NCRs is a cornerstone for achieving operational efficiency and sustaining high-quality standards. By recognizing the value of NCRs and adhering to robust management practices, organizations can navigate compliance challenges and drive significant improvements that resonate throughout their operations. The path to operational excellence is paved with a commitment to quality, and NCRs are integral to this journey.