Understanding the LVD Directive 2014/35/EU: A Comprehensive Tutorial for Manufacturers
Explore the LVD Directive 2014/35/EU and its compliance essentials for manufacturers.
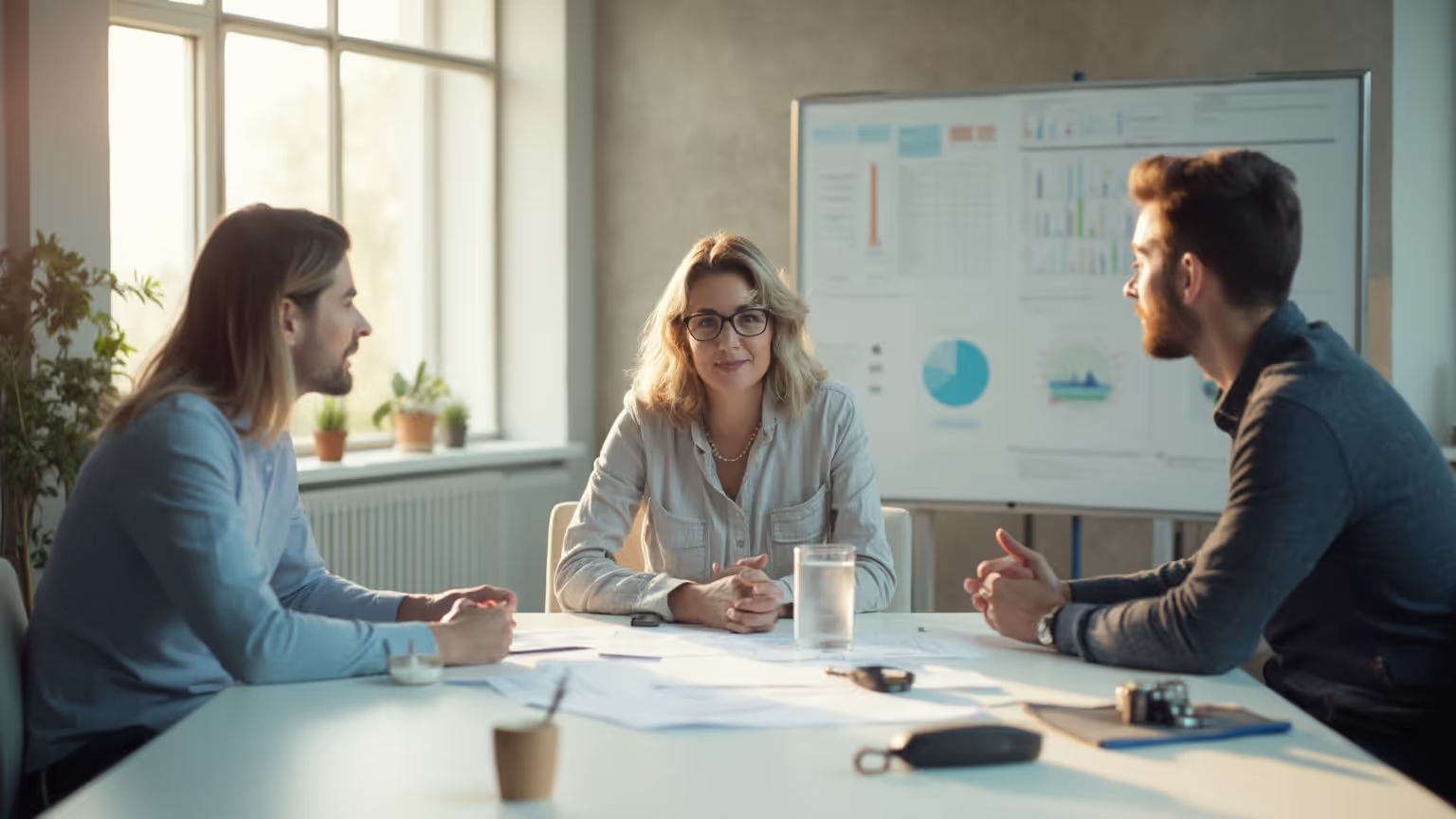
Overview:
The LVD Directive 2014/35/EU is essential for manufacturers as it establishes safety and quality standards for electrical equipment operating within specified voltage ranges, ensuring user protection and compliance with EU regulations. The article underscores the importance of adherence to this directive by detailing the necessary compliance requirements, risk assessment procedures, and the significant consequences of non-compliance, such as safety hazards and regulatory penalties, highlighting the growing emphasis on sustainability and digital tools in the compliance landscape.
Key Highlights:
- The LVD 2014/35/EU regulates electrical equipment operating between 50-1,000 volts AC and 75-1,500 volts DC to ensure user safety and product quality.
- Manufacturers must comply with strict design, technical documentation, and labeling requirements to avoid safety risks and regulatory penalties.
- CE marking indicates compliance with EU safety standards, enhancing consumer trust and facilitating market access.
- Risk assessment involves identifying hazards, evaluating risks, implementing control measures, and documenting findings to ensure ongoing safety.
- Manufacturers face challenges such as complex regulations, resource constraints, and high testing costs, which can hinder compliance efforts.
- Future trends include a focus on sustainability, digital compliance tools, global standard harmonization, and increased consumer demand for transparency.
Introduction
The Low Voltage Directive (LVD) 2014/35/EU stands as a fundamental regulation within the European Union, designed to ensure the safety of electrical equipment operating within specific voltage ranges. As manufacturers navigate the complexities of compliance, understanding the implications of the LVD becomes paramount—not only for safeguarding users from potential hazards but also for maintaining a competitive edge in the marketplace.
This article delves into the essential requirements and challenges manufacturers face under the LVD, highlighting the importance of:
- Risk assessment
- Technical documentation
- CE marking
Furthermore, it explores emerging trends that are shaping the future of compliance, emphasizing the need for manufacturers to adapt their strategies in response to evolving regulatory landscapes and consumer demands. By embracing these insights, organizations can enhance product reliability and foster greater consumer trust, ultimately driving success in a highly regulated environment.
Overview of the Low Voltage Directive 2014/35/EU
The lvd directive 2014/35/eu serves as a cornerstone regulation within the European Union, designed to protect the well-being of electrical equipment that operates within defined voltage ranges (50 to 1,000 volts for alternating current and 75 to 1,500 volts for direct current). This directive is crucial in safeguarding users from possible electrical dangers, ensuring that items comply with rigorous quality standards. Producers are required to create and build their items in accordance with the lvd directive 2014/35/eu, which not only guarantees security but also promotes the smooth flow of goods within the EU market.
As Krista Alasalmi, a testing expert, points out, 'And when checks are conducted, they frequently result in shocking findings, such as the cadmium jewelry and high-phthalate-content plastic we’ve discussed here.' This emphasizes the critical nature of compliance, as non-adherence can lead to serious safety concerns and regulatory repercussions. For instance, in 2023, Mercedes-Benz was identified as a dangerous car brand with 47 serious risk alerts, illustrating the severe consequences of non-compliance.
Furthermore, manufacturers must ensure that their packaging aligns with labeling requirements, including the appropriate use of symbols like the WEEE label. Additionally, importers and manufacturers of electronic devices must register with national EU authorities, adhering to specific national rules and procedures to comply with the lvd directive 2014/35/eu and facilitate market surveillance. Comprehending the lvd directive 2014/35/eu is essential for manufacturers seeking to reduce risks, improve reliability, and ultimately boost customer satisfaction and brand reputation.
Incorporating the Process Capability Index (CPK), a statistical measure of a process's ability to produce output within specified limits, into quality assurance practices can help D2C brands measure their process performance and capability, thereby minimizing defects. With data from Return Logic indicating that 60% of returns stem from preventable quality issues, leveraging OpsNinja's on-site inspections can significantly reduce this rate, protecting brands from negative reviews—94% of customers have avoided making a purchase due to a bad review—thereby reinforcing their market position. In light of recent data indicating a high incidence of non-compliant items in the market, adherence to the lvd directive 2014/35/eu has never been more crucial.
Key Compliance Requirements for Manufacturers under the LVD
Manufacturers must navigate several essential compliance requirements under the LVD directive 2014/35/EU to ensure the reliability and efficacy of their electrical items. These requirements include:
- Product Design and Construction: Products must be meticulously designed and constructed to prioritize safety, effectively reducing dangers associated with electrical shock, overheating, and fire hazards.
A comprehensive evaluation of potential dangers associated with the product's use is crucial. This process not only assists in identifying inherent dangers but also supports in executing strategies to remove or lessen them, aligning with best practices outlined by regulatory specialists. In fact, 52% of regulatory specialists believe that a lack of data and information about partners exposes businesses to third-party challenges, emphasizing the importance of thorough adherence practices.
-
Technical Documentation: Manufacturers are required to prepare and maintain thorough technical documentation that demonstrates compliance with the LVD. This documentation should include detailed design calculations, risk assessments, and relevant test reports to ensure transparency and accountability.
-
Conformity Assessment: Depending on the category of the item, manufacturers may need to undergo specific conformity assessment procedures.
This could involve testing by notified bodies to confirm adherence to all applicable standards.
- CE Marking: Affixing the CE marking to items signifies their conformity with the LVD and other pertinent EU regulations. This marking acts as an essential sign of security and adherence, fostering consumer confidence.
Non-adherence can result in serious consequences, including recalls, financial penalties, and irreversible harm to brand reputation. As highlighted by Return Logic, 60% of returns are due to preventable quality issues, which can be caught early through on-site inspections, reducing returns by up to 60% and protecting your brand image. Furthermore, it is observed that 94% of customers refrain from making purchases due to unfavorable reviews, highlighting the significance of upholding high product quality and strong compliance efforts to protect customer trust.
Moreover, products must include instructions and informational content in a language comprehended by consumers, in line with the national languages of each EU member nation. This requirement ensures that consumers have access to essential safety information, promoting safe usage of electrical equipment.
Understanding Risk Assessment Procedures
To effectively carry out a threat evaluation under the Low Voltage Directive (LVD), manufacturers should follow these essential steps:
- Identify Hazards: Conduct a comprehensive evaluation of all potential hazards associated with the product throughout its lifecycle. This includes examining phases such as design, manufacturing, usage, and disposal. For example, identifying electrical hazards during the design phase can prevent costly modifications later.
- Evaluate Hazards: Analyze the dangers associated with each identified threat. This involves assessing both the likelihood of occurrence and the potential severity of harm. The use of statistical techniques, like the chi-square test at a significance level of 0.05, can offer valuable insights into the probability of factors appearing in electrical equipment.
- Implement Control Measures: Develop and implement strategies to reduce identified threats. This may involve redesigning the product, incorporating extra protective features, or ensuring that clear instructions and warnings are provided to users. Continuous monitoring and regular reviews of these measures are vital for maintaining their effectiveness. A case study on the continuous monitoring of evaluations underscores the necessity of such practices to ensure ongoing safety improvements.
- Document Findings: Maintain thorough documentation of the entire assessment process. This should encompass the methodologies utilized, the results achieved, and any measures implemented to reduce hazards. Comprehensive records are crucial for demonstrating compliance with the LVD directive 2014/35/EU and for supporting any future evaluations or audits. As Thomas L. Saaty aptly states,
This study was based on the method suggested by Chang because it is more comfortable to conduct than other approaches and supplies accurate outputs.
This emphasizes the significance of choosing effective approaches for documenting and evaluating uncertainties. By following these steps, manufacturers can improve their item security protocols and align with current best practices in risk evaluation.
The Role of CE Marking in Compliance
CE marking serves as a critical indicator that an item adheres to the safety, health, and environmental protection standards set by the European Union. Established in March 1994, when the EU and EFTA signed an agreement creating the European Economic Area, CE marking plays a vital role in allowing access to the Single Market and its advantages. To successfully obtain CE marking, manufacturers should follow these essential steps:
- Ensure Compliance: It is vital to confirm that the item aligns with all relevant EU directives, specifically the lvd directive 2014/35/eu.
- Compile Technical Documentation: Manufacturers must gather comprehensive documentation demonstrating compliance.
This includes design specifications, risk assessments, and test results, which collectively validate the safety of the item. - Declare Conformity: A Declaration of Conformity must be created, clearly stating that the item complies with all applicable EU regulations.
This document is a formal confirmation of adherence and is critical for regulatory purposes. - Affix the CE Mark: Once compliance is validated, the CE mark should be affixed to the item in a manner that is both visible and legible.
This marking not only facilitates the item's entry into the EU market but also significantly enhances consumer trust in the brand's commitment to safety and quality.
As noted by the European Roundtable of Industrialists (ERT) in their memorandum titled 'Foundations for the Future of European Industry,' CE marking is essential for fostering confidence among consumers and businesses alike. The process is crucial as it aligns with the EU's regulatory framework and reflects a brand's dedication to delivering safe and reliable electrical goods.
Furthermore, the Commission's Green Paper on European Standardization emphasized the need for a common marking system to reduce confusion and enhance consumer confidence in the European market. This ultimately fosters greater consumer trust, which is paramount for brand loyalty and success.
Common Challenges in LVD Compliance
Manufacturers frequently confront a variety of challenges in the pursuit of adherence to the LVD directive 2014/35/EU, significantly impacting their operational efficacy and product quality assurance. Key obstacles include:
-
Complex Regulatory Landscape: The extensive array of EU regulations creates a daunting adherence environment.
Manufacturers must diligently monitor regulatory updates to ensure adherence, with 67% of global executives expressing that ESG regulation is overly complex, and 70% indicating a desire for clearer guidance from regulators. The evolving nature of these regulations adds to the complexity, as manufacturers must continuously adapt to new requirements. -
Resource Constraints: Smaller manufacturers often grapple with limited resources and expertise necessary for effective evaluations.
This issue is exacerbated by findings from the Coalfire Report 2023, where 27% of security and IT professionals ranked mitigating internal audit fatigue from recurring second-party and third-party assessment activities as the top regulatory program challenge. This highlights the significant resource constraints faced by manufacturers. -
Documentation Requirements: The obligation to maintain thorough and accurate documentation can be burdensome, yet it is vital for demonstrating compliance.
Manufacturers must allocate sufficient time and effort to meet these documentation standards to avoid potential penalties. -
Testing and Certification Costs: The financial burden of evaluating items and securing certifications can be substantial, particularly for smaller brands that may struggle to absorb these costs. Non-destructive testing (NDT) can be a valuable approach in this regard, allowing for thorough assessments without damaging products, thus enhancing quality assurance in the supply chain.
This financial aspect is essential, as many manufacturers find it challenging to balance regulatory costs with operational budgets. -
Regulatory Changes: The Lifts Directive, as highlighted by the LVD directive 2014/35/EU, applies to lifts serving buildings for transporting persons and goods, including safety components, underscoring the evolving nature of regulations impacting LVD compliance.
-
Role of Process Capability Index (CPK): Understanding and utilizing the Process Capability Index (CPK) is essential for D2C brands aiming to maintain high-quality standards.
A robust CPK can indicate a process's ability to produce outputs within specified limits, thereby enhancing product quality and ensuring compliance with the LVD directive 2014/35/EU.
To effectively navigate these challenges, manufacturers can benefit from strategies such as partnering with regulatory consultants, investing in staff training, and leveraging digital tools that streamline documentation and testing processes. Insights from the case study titled 'Obstacles to Addressing Compliance Risks' reveal that the top obstacles to confidence in managing regulatory risks include a lack of knowledgeable personnel, inadequate resources, and poor company culture. These approaches can help mitigate the impact of resource constraints and enhance overall regulatory outcomes.
Future Trends in LVD Compliance
As the regulatory environment regarding adherence to the LVD directive 2014/35/EU continues to evolve, manufacturers must stay ahead of emerging trends that will influence their adherence strategies. Key trends to monitor include:
- Increased Focus on Sustainability: Regulatory bodies are progressively emphasizing the environmental impacts of manufacturing processes.
Consequently, stricter requirements are being implemented concerning energy efficiency and responsible material sourcing, aligning with the broader sustainability initiatives observed across industries. Notably, renewable generation at a scale required to power a manufacturing facility occupies significant space, highlighting the sustainability challenges manufacturers face. Companies that adapt to the LVD directive 2014/35/EU not only ensure compliance but also position themselves advantageously in the marketplace.
As mentioned by Alyssa Zucker, Senior Industry Principal, by acting now and aligning with current and emerging sustainability regulations, your company can guarantee adherence and drive competitive advantages while also leading the charge toward a more sustainable and resilient future.
- Digital Compliance Tools: The integration of advanced digital tools is transforming the adherence process.
These technologies improve documentation precision, simplify risk evaluations, and aid product testing, making it easier for manufacturers to meet regulatory requirements efficiently. Adoption rates of these digital tools are increasing, reflecting their growing significance in upholding standards.
-
Global Harmonization of Standards: With the expansion of international trade, there is a significant movement toward aligning regulations across regions. This trend requires that manufacturers adjust their adherence strategies to meet different regulatory demands while ensuring the security of offerings across various markets.
-
Consumer Demand for Transparency: Today's consumers are increasingly educated about product safety and sustainability, driving a demand for transparency from brands regarding their adherence and safety measures. Manufacturers are encouraged to foresee this change and integrate clear communication regarding their adherence strategies to foster consumer trust.
-
Emerging Sustainability Initiatives: As sustainability regulations become more standardized, the shift from voluntary to mandatory disclosures highlights the need for manufacturers to adopt proactive sustainability measures. Dr. Kelly Scanlon, IPC's lead sustainability strategist, recently conducted interviews with industry leaders during IPC APEX EXPO 2024, discussing various approaches to sustainability in electronics. Case studies, including the report titled 'The Road Ahead for Sustainability Regulations,' indicate that companies aligning with these regulations can secure a competitive edge while contributing positively to environmental goals.
The report highlights that those who adopt these changes will not only guarantee adherence but also pave the path in promoting a more sustainable future for the industry.
By acknowledging these trends and integrating them into their compliance strategies, manufacturers can maintain their competitiveness while enhancing consumer trust.
Conclusion
Manufacturers operating within the framework of the Low Voltage Directive (LVD) 2014/35/EU face a complex yet crucial landscape that demands a thorough understanding of compliance requirements. The directive's emphasis on risk assessment, technical documentation, and CE marking underscores the necessity of prioritizing safety and quality in electrical equipment. As highlighted, proactive risk management and meticulous product design are pivotal in minimizing potential hazards, thereby not only ensuring compliance but also enhancing product reliability and consumer trust.
Navigating the challenges of compliance, including resource constraints and evolving regulations, requires strategic approaches such as leveraging digital tools and fostering a culture of continuous improvement. The insights shared indicate that staying informed about regulatory changes and emerging trends, particularly around sustainability and consumer transparency, will be essential for manufacturers aiming to maintain a competitive edge in the marketplace.
In conclusion, adherence to the LVD is not merely a regulatory obligation; it is an opportunity for manufacturers to reinforce their commitment to safety, quality, and sustainability. By embracing these principles, organizations can foster greater consumer confidence, ultimately driving success in a highly regulated environment. The path forward is clear: manufacturers must adapt, innovate, and prioritize compliance to thrive in the ever-evolving landscape of electrical equipment safety.